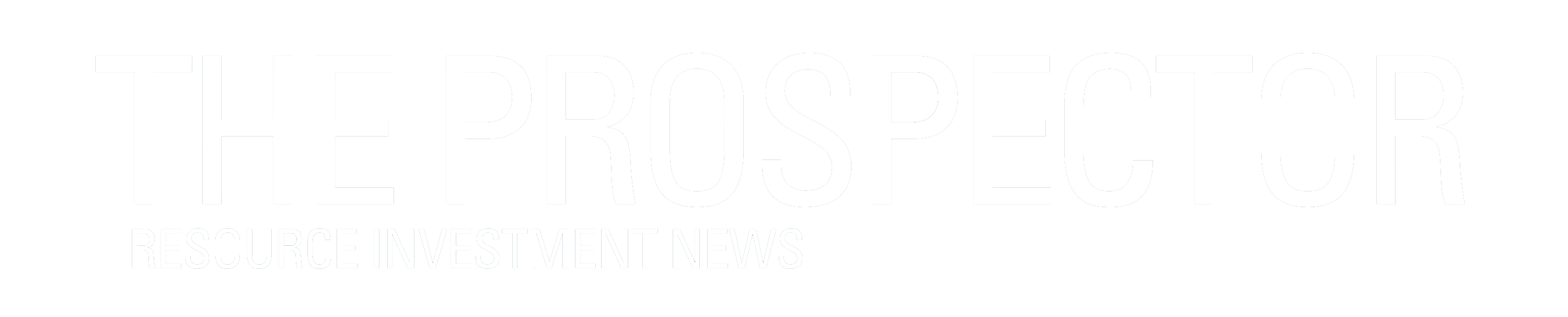
Titan Mining Corporation (TSX: TI) is pleased to announce the Phase III metallurgy results conducted at SGS Lakefield for the Kilbourne graphite project. The Company is also excited to be outlining parameters of a processing facility for Kilbourne natural graphite mineralized material, to be co-located with the Company’s existing zinc operations at Empire State Mines. This initiative aims to fast-track development of Kilbourne and make ESM the first end to end producer of natural flake graphite in the United States since the 1950s.
Highlights:
Don Taylor, CEO of Titan commented: “We are pleased with the Phase III test results demonstrating potential closed-circuit recoveries of 90%+ and high-grade concentrate product from Kilbourne. The current resource outlined at Kilbourne represents only 8,300 ft of strike length tested of a total strike length of 25,000 ft. Kilbourne has significant resource expansion potential to meet the demands of US natural flake graphite over a long- term period and we are excited to be moving towards the next phase of development”.
Rita Adiani, President of Titan commented: “The Phase III test results and size fraction analysis provides us with useful product data as we commence scoping out pricing and relevant US customer base for Kilbourne graphite. The Facility is the first step towards ESM becoming the first end to end producer of natural flake graphite in the United States and having the ability to secure supply chain resilience for our core industries such as semiconductors, military spec graphite and batteries whilst having domestic resources to support industrial uses which currently rely fully on imports. We are excited by current developments as we surface more shareholder value through organic growth”.
Phase III Metallurgy Results and Proposed Flow Sheet
A process optimization program was recently completed at SGS Minerals in Lakefield, Ontario. The samples that were used for the optimization program included a total of 118 mineralized intervals from drill holes KX23-001, KX24-002, KX24-003, and KX24-004. The drill core intervals were divided to generate four (4) variability composites, namely North Shallow, North Deep, South Shallow, and South Deep. Further, sub-samples of all 118 drill core intervals were combined to produce a Master composite for optimization testing. Once optimization testing was completed, the variability samples were subjected to the optimized flowsheet and conditions to confirm its robustness.
Total grade and graphitic head grade for the Master composite and the four variability composites are presented in Table 1. Graphitic carbon grades were only slightly lower than total carbon grades, which suggests low concentrations of organic and carbonate carbon in the samples.
Table 1: Head Grades of Master and Variability Composites
Composite | Assays (%) | |
C(t) | C(g) | |
Master | 3.48 | 3.14 |
North Shallow | 3.38 | 3.21 |
South Shallow | 3.51 | 3.28 |
North Deep | 2.87 | 2.68 |
South Deep | 3.57 | 3.25 |
Notes: C(t): Total Carbon C(g): Graphitic Carbon
A total of eight (8) cleaner flotation tests were completed. Process variables that were evaluated included flash/rougher circuit configuration, primary grind size, regrind technologies and the number of regrind steps. A standard reagent suite consisting of diesel and methyl isobutyl carbinol (MIBC) was chosen since it was effective in previous programs.
The optimization program produced the flowsheet that is depicted in Figure 1. The flowsheet comprised a primary grind to P80 = 100 microns followed by rougher flotation. The rougher concentrate is upgraded in a cleaning circuit consisting of one polishing mill and three stirred media mills (SMM) followed by cleaner flotation after each regrind step. The final concentrate is dewatered, dried, and then bagged.
Figure 1: Simplified Facility Flowsheet
The last master composite test with the optimized conditions (Test F8) produced a final concentrate of 98.8% C(t) at an open circuit graphite recovery of 87.3%. This recovery is expected to increase during commercial operation since intermediate tailings streams are cycled rather than being treated as final tailings. A closed-circuit graphite recovery of 90-91% is projected based on the graphite losses to intermediate tailings streams.
The four variability flotation tests produced concentrate grades between 97.6% C(t) for the North Shallow and 99.3% C(t) for the South Deep composite. The open circuit graphite recovery ranged between 82.3% for the North Shallow composite and 92.4% for the North Deep composite. These results are well aligned with the Master composite and confirm the consistent metallurgical performance of the Kilbourne graphite mineralization and the robustness of the proposed flowsheet and conditions.
The final concentrates were submitted for a size fraction analysis to quantify the flake size distribution and total carbon grade profile. The results are summarized in Table 2.
Table 2: Size Fraction Analysis of Final Concentrate of the Master and Variability Composites
Product Size (Mesh) |
Master | North Shallow | North Deep | South Shallow | South Deep | |||||
Mass (%) |
% C(t) |
Mass (%) |
% C(t) |
Mass (%) |
% C(t) |
Mass (%) |
% C(t) |
Mass (%) |
% C(t) |
|
100 | 8.2 | 98.1 | 2.2 | 95.1 | 8.3 | 96.9 | 3.8 | 96.5 | 9.2 | 97.4 |
150 | 11.7 | 98.9 | 6.9 | 97.9 | 12.4 | 99.2 | 9.5 | 99.7 | 10.1 | 99.4 |
200 | 26.0 | 99.1 | 22.7 | 97.8 | 24.3 | 99.0 | 24.2 | 98.2 | 22.1 | 99.3 |
-200 | 54.1 | 99.2 | 68.2 | 97.7 | 55.1 | 99.1 | 62.5 | 98.6 | 58.6 | 99.3 |
The Facility
Titan is in the final phases of completing engineering in respect of the Facility. The Facility is expected to produce 1,000-1,200t per annum of graphite concentrate and aims for modular expansion to baseline production of 40,000t per annum with further growth capability. The Facility will be fed Kilbourne mineralized material and will be co-located in the ESM mill area. It will benefit from leveraging personnel and infrastructure from the existing zinc ESM mill operations thereby reducing capital and operating costs.
The key objectives of the commercial demonstration facility are:
As of 2024, the global market for natural flake graphite across the product segments the Company is targeting, was assessed to be 1.7 mt per annum. ESM is therefore well positioned to service global demands of natural flake graphite.
Based on available operating cost data for the Facility and pricing metrics across various targeted product groups, ESM is targeting a 40-45% operating margin for its full production facility of 40,000t per annum (based on an average sales price of US$2350/t).
Equipment for the Facility together with associated installation costs and working capital is likely to cost US$6.0-7.5 million. Titan has commenced work on various funding initiatives for this project.
Kilbourne Graphite Market Applications
The market applications for natural flake graphite production from the Facility comprise of the below key product groups. Strategic introduction timelines will be coordinated with the Facility production ramp up and customer qualifications. Micronized STD Purity (95.0% LOI MIN) products are planned to expand progressive qualifications and add to revenues and margins. Future high purity (99.9% LOI MIN) micronized graphite products are anticipated to further enhance both revenues and margins to the Company targeting primary and secondary batteries, medical device, military specifications and nuclear grade graphite.
Initial concentrate product applications from the facility will target thermal management, engineered products and lubricants followed by high-purity engineered products (including nuclear graphite) and energy storage products (battery- CSPG anode grades and primary alkaline).
Key customers for Micronized STD Purity graphite are expected to comprise producers of the following:
Quality Assurance and Quality Control
All work and chemical analysis was conducted at SGS Lakefield in Canada, which is independent of the Company. This laboratory is ISO/IEC 17025 accredited, which ensures that the laboratory produces high-quality, accurate, and timely results. Repeat analyses of flotation products were completed as per the internal SGS QA/QC protocol. The QP is not aware of any factors that could materially affect the accuracy or reliability of the data referred to herein.
Qualified Person
The scientific and technical information in this news release has been reviewed and approved by Mr. Oliver Peters, a Principal Metallurgist and President of Metpro Management Inc., with over 25 years of mineral processing experience. He is a Qualified Person within the meaning of NI 43-101 and is independent of the Company. Mr. Peters is satisfied that the metallurgical testing procedures and associated assay methods used are standard industry operating procedures and methodologies. He has reviewed, approved and verified the technical information disclosed in this news release, including core sampling, analytical and test data underlying the technical information.
About Titan Mining Corporation
Titan is an Augusta Group company which produces zinc concentrate at its 100%-owned Empire State Mine located in New York state. The Company is focused on value creation and operating excellence, with a strong commitment to developing critical mineral assets that enhance the security of the U.S. supply chain. For more information on the Company, please visit our website at www.titanminingcorp.com.
Superior drilling results continue to exceed the Company’s expe... READ MORE
American Lithium Corp. (TSX-V:LI) (OTCQX:AMLIF) (Frankfurt:5LA1) ... READ MORE
North Peak Resources Ltd. (TSX-V: NPR) (OTCQB: NPRLF) announces t... READ MORE
InZinc Mining Ltd. (TSX-V: IZN) is pleased to report the first re... READ MORE
Fortuna Mining Corp. (NYSE: FSM) (TSX: FVI) is pleased to report ... READ MORE