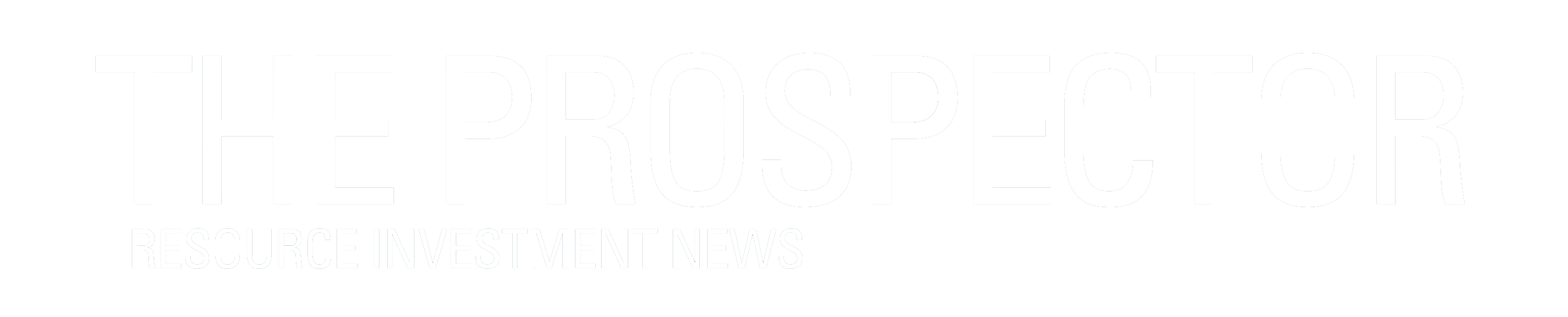
Eldorado Gold Corporation (TSX: ELD) (NYSE: EGO) reports the Company’s financial and operational results for the third quarter of 2024. For further information, please see the Company’s Consolidated Financial Statements and Management’s Discussion and Analysis filed on SEDAR+ at www.sedarplus.com under the Company’s profile.
Third Quarter 2024 Highlights
Operations
Financial
Corporate
“As gold prices reached record highs during the quarter we continued to realize margin expansion and strong cash flow generation across our operations,” said George Burns, President and Chief Executive Officer. “Free cash flow before Skouries investment totalled $98.3 million.”
“At Olympias, we successfully concluded the CBA negotiations and reached a mutually beneficial agreement with the union workforce in early August. This three-year agreement combined with increased productivity in our underground operations, and as contemplated in our guidance, supports the 650ktpa expansion, an increase from 500ktpa, positioning Olympias for long-term profitability over its current mine life of 15 years. In Canada, at Lamaque, progress continued on the Ormaque bulk sample. We have begun stockpiling material ahead of processing it through the mill in the fourth quarter and remain on track to declare an inaugural reserve later this year.”
“At Kisladag, we encountered a few operational challenges including lower tonnes stacked, slightly lower recovery and a longer leach cycle than planned. Throughout the quarter, we implemented a number of improvements to address these issues. This included improving the stacking sequence where we have started to see positive results. In addition, we have begun to see improved solution management through various innovative methods that are being deployed to help draw down the gold inventory.”
“Production reached 364,625 ounces in the first nine months of the year, an increase of 7% compared to 2023, and 12% compared to 2022, respectively. We are on track to meet our 2024 production and cost guidance. We have tightened the gold production range to between 505,000 to 530,000 ounces. As gold prices hit record highs in the third quarter, we continued to experience increased royalty costs, which has impacted our overall costs, and we expect full year all-in sustaining costs to be near the upper end of guidance of between $1,260 and $1,290 per ounce.”
“Our transformational Skouries project continues to track on budget and on schedule with first production expected in the third quarter of 2025. Solid progress was made during the third quarter, with overall project completion currently at 79%. As anticipated, the contract was awarded for the steel and mechanical installations for the filter building during the quarter, which is part of the critical path. Thus far the construction workforce productivity is slightly beating our assumptions. With approximately 1,000 personnel working, we are making steady progress towards our year-end target of 1,300. Our focus once we have the additional personnel onsite will turn to integrating them at our assumed productivity levels to maintain the schedule and budget. We are managing this closely and taking proactive measures to mitigate potential challenges in a tight construction labour market. To view the progress see our Q3 2024 progress update video linked below.”
Q3 2024 progress update video link: https://youtu.be/js0MxV8Dgdo
Skouries Highlights
Growth capital invested totalled $82.7 million in Q3 2024 and $227.1 million during the nine months ended September 30, 2024. At September 30, 2024, the growth capital invested towards the overall capital estimate of $920 million totalled $411.9 million.
In 2024, the expected capital spend has been lowered to between $350 and $380 million from the original guidance of $375 and $425 million. The lowered capital is not expected to impact first production as it is primarily related to rescheduled work that has been shifted to a later phase of the project that is not on the critical path, and reflects a slower than expected ramp-up of contractor mobilization during the first three quarters of 2024.
First production of the copper-gold concentrate is expected in Q3 2025, with expected 2025 gold production of 50,000 to 60,000 ounces and copper production of 15 to 20 million pounds. The project remains on track for commercial production at the end of 2025.
Table 1: Skouries Project – Project Expenditures (January 1, 2023 to September 30, 2024)
Millions of US$ | As of September 30, 2024 |
Total capital estimate | $920 |
Expenditures incurred since project restart | 412 |
Remaining spend | 508 |
Committed expenditures – including expenditures incurred | 788 |
Uncommitted expenditures | 132 |
Construction Activities
Overall construction progress is 79% when including the first phase of construction.
Work continues to advance on the filtered tailings building which is on the critical path. In September, the first contract for the filtered tailings building was awarded for the structure and mechanical installations. For efficiency, the contract was split into two components:
1) | filtered tailings building structure and mechanical installations, and | |
2) | piping, electrical and instrumentation. | |
Piling has been completed for the filtered tailings building and concrete work is progressing to enable construction of the structural steel. With three active drills on site, the piles for the filtered tailings facility ancillary buildings continue to progress. To date, 388 piles have been completed out of a total of 871. As previously announced, the fabricated frames for the filter press plates arrived on site during Q2 2024, and all filter press components have now been delivered to site.
Primary Crusher Building
Progress continued to advance on the foundation construction of the primary crusher with retaining walls and stabilized excavations nearing completion. Construction of the crusher building structure will commence in November.
Process plant
Work in the process plant continues to progress. Re-lining of the flotation tanks was completed as planned and structural and mechanical work is in progress. Off-site pipe spool fabrication continues and delivery of high-density polyethylene piping to site has commenced. Scaffolding is advancing to support electrical cable tray and piping installations and the contractor continues to ramp up to support increasing levels of activity. Work has also commenced on support infrastructure including the process control room building, process plant sub-station, water pump station, lime plant, air blowers building, compressor building and flotation reagent areas.
Thickeners
Construction of the three thickeners progressed on plan during the quarter. Major concrete pours are complete for the foundations of the first two thickeners. Support columns are complete on the first thickener and over 50% complete for the second thickener. Construction of the third thickener will start in Q4 2024 following completion of the first thickener.
Integrative Extractive Waste Management Facility (the “IEWMF”)
During Q3 2024, construction continued to progress at the coffer dam site with excavation of the spillway and foundation preparation. By the end of 2024, the Company expects to have completed the first of two water management ponds, coffer dam and significantly advanced the earthworks. Work continues to progress with foundation preparation for the KL Embankment (tailings embankment) and the fill placement for water management pond 2 has advanced on plan for completion at year end. Excavations for water management pond 1 continue and development of the low-grade ore stockpile advanced with foundation preparation, drain construction and fill placement.
Underground Development
Progress has been made on the underground with expansion of the underground services for water management, ventilation and electrical distribution. Approximately 70% of the equipment and operator licenses have been received to date and development mining is ramping up. Access to the test stopes is advancing at the upper level as planned and the priority for the balance of the year is to advance the main decline and gain access to the bottom elevations of the test stopes. The schedule to receive all licenses and permits was later than planned and while the contractor is ramping up, it has delayed the completion of the expected 2,200 metres of underground development for 2024. The underground development for 2024 is now expected to be between 500 and 600 metres. While the metres are not on track with guidance the underground is not on the critical path for first production, in addition, this does not impact the overall timing for the two test stopes which are expected to be completed in Q3 2025.
Engineering, Procurement and Operational Readiness
Engineering
As engineering works are now at 78% and are nearing substantial completion, the focus has been on finalizing engineering to support the construction schedule. The release of structural steel for fabrication is nearing completion and steel deliveries have commenced to site to support steel construction in the process plant and filtered tailings building.
Procurement
At the end of Q3 2024, procurement is substantially complete, with all long-lead items procured and the focus on managing fabrication and deliveries.
Operational Readiness
A key focus of the operational readiness team is to establish a strong, risk-based operational readiness plan. Key departmental plans have been developed, an overarching governance framework established, and weekly leadership forums and monthly steering committee reviews established. Specialized support has been engaged to focus on processing operationalization, and readiness support. Further work is ongoing to establish detailed readiness plans for support and shared services. Priority focus areas have been identified and resource allocation adjusted accordingly.
The development of the Management Operating System (MOS) is currently focused on providing frontline supervisor and worker practices and procedures to the open pit operations team. These practices and procedures are established to ensure adherence to standards as well as establishing best practices and overall transparency across planning, execution, reporting and remediation to the frontline team. Several workshops were held with the heads of functions and initial departmental workflows were established.
The training department’s short-term priority was developing a training plan for the open pit excavation activities in line with the recently adopted competency-based framework. The competency-based framework identifies specific competencies per role and then assesses the employee’s performance against specific performance criteria on knowledge, skills and attitude. This competency-based framework will ensure improved individual performance compared to the previous time in role-based competency framework only. Training material as well as training providers are in place and four (4) CAT 6020B hydraulic excavator operators commenced training during October 2024. This program will be expanded with the arrival of additional mining equipment in H1 2025. The Mavres Petres main training building structural upgrade has been completed and the focus for the coming quarter will be to equip practical training workbenches for basic skills training and assessment as well as for refresher training.
Operations
The operations team completed their labour strategy and associated organizational designs. Recruitment is underway at local and national levels. Several local and national job fairs are planned for Q4 2024 to attract as many as possible potential employees.
The CAT 6020B hydraulic excavator was assembled during the quarter and training of operators commenced in October 2024. Most of the remaining open pit mining fleet will arrive during H1 2025. The first operational plan was prepared that combines the completion of construction pre-stripping and the start of open pit mining in H1 2025. A similar plan is being prepared for the underground mine and the expectation is that both the surface and underground mining will be operationalized during Q4 2024.
Other operational, commercial and administrative departments made progress in recruiting their leadership and supervision employees and setting up operating and commercial processes.
Workforce
In addition to the Operational Readiness team, as at September 30, 2024, there were approximately 1,000 personnel working. Thus far the construction workforce productivity is slightly ahead of our assumptions. We are making steady progress towards our year-end target of 1,300 workers on site. Our focus once we have the additional personnel onsite will turn to integrating them at our assumed productivity levels to maintain the schedule and budget. We are managing this closely and taking proactive measures to mitigate potential challenges in a tight construction labour market.
Skouries key milestones in 2024, which include:
Area of Focus | Key Milestone | Status |
Procurement and Engineering |
|
|
Process Plant |
|
|
|
|
|
Filtered Tailings Facility |
|
|
Integrated Extractive Waste Management Facility (“IEWMF”) |
|
|
Underground |
|
|
|
|
|
Consolidated Financial and Operational Highlights
3 months ended September 30, | 9 months ended September 30, | ||||||||||||
2024 | 2023 | 2024 | 2023 | ||||||||||
Revenue | $331.8 | $244.8 | $886.9 | $701.6 | |||||||||
Gold produced (oz) | 125,195 | 121,030 | 364,625 | 341,973 | |||||||||
Gold sold (oz) | 123,828 | 119,200 | 361,062 | 339,151 | |||||||||
Average realized gold price ($/oz sold) (2) | $2,492 | $1,879 | $2,309 | $1,920 | |||||||||
Production costs | 141.2 | 115.5 | 392.0 | 341.3 | |||||||||
Total cash costs ($/oz sold) (2,3) | 953 | 794 | 939 | 858 | |||||||||
All-in sustaining costs ($/oz sold) (2,3) | 1,335 | 1,177 | 1,310 | 1,225 | |||||||||
Net earnings (loss) for the period (1) | 95.0 | (8.0 | ) | 184.1 | 12.2 | ||||||||
Net earnings (loss) per share – basic ($/share) (1) | 0.46 | (0.04 | ) | 0.90 | 0.06 | ||||||||
Net earnings (loss) per share – diluted ($/share) (1) | 0.46 | (0.04 | ) | 0.90 | 0.06 | ||||||||
Net earnings (loss) for the period continuing operations (1,4) | 101.1 | (6.6 | ) | 192.7 | 14.4 | ||||||||
Net earnings (loss) per share continuing operations – basic ($/share)(1,4) |
0.49 | (0.03 | ) | 0.95 | 0.07 | ||||||||
Net earnings (loss) per share continuing operations – diluted ($/share)(1,4) |
0.49 | (0.03 | ) | 0.94 | 0.07 | ||||||||
Adjusted net earnings continuing operations – basic (1,2,4) | 71.0 | 35.0 | 192.9 | 61.4 | |||||||||
Adjusted net earnings per share continuing operations ($/share)(1,2,4) |
0.35 | 0.17 | 0.95 | 0.32 | |||||||||
Net cash generated from operating activities (4) | 180.9 | 108.1 | 388.4 | 223.3 | |||||||||
Cash flow from operating activities before changes in working capital (2,4) | 166.5 | 97.5 | 407.0 | 273.1 | |||||||||
Free cash flow (2,4) | (4.8 | ) | (19.3 | ) | (67.8 | ) | (76.4 | ) | |||||
Free cash flow excluding Skouries (2,4) | 98.3 | 37.3 | 165.8 | 30.7 | |||||||||
Cash, cash equivalents and term deposits (4) | 676.6 | 476.6 | 676.6 | 476.6 | |||||||||
Total assets | 5,565.1 | 4,812.2 | 5,565.1 | 4,812.2 | |||||||||
Debt (4) | 849.2 | 596.5 | 849.2 | 596.5 |
(1) | Attributable to shareholders of the Company. | |
(2) | These financial measures or ratios are non-IFRS financial measures or ratios. See the section ‘Non-IFRS and Other Financial Measures and Ratios’ of our MD&A for explanations and discussions of these non-IFRS financial measures or ratios. | |
(3) | Revenues from silver, lead and zinc sales are off-set against total cash costs. | |
(4) | Amounts presented for 2024 and 2023 are from continuing operations only and exclude the Romania segment. See Note 4 of our condensed consolidated interim financial statements for the three and nine months ended September 30, 2024. | |
Total revenue increased to $331.8 million in Q3 2024 from $244.8 million in Q3 2023 and to $886.9 million in the nine months ended September 30, 2024, from $701.6 million in the nine months ended September 30, 2023. The increases in both three and nine-month periods were primarily due to the higher average realized gold price as well as the higher sales volumes.
Production costs increased to $141.2 million in Q3 2024 from $115.5 million in Q3 2023 and to $392.0 million in the nine months ended September 30, 2024 from $341.3 million in the nine months ended September 30, 2023. Increases in both periods were driven primarily by higher sales volume as well as higher cash costs, the latter impacted by higher royalty expense due to higher gold sales and higher gold price, as well as increases in labour costs.
Total cash costs3 averaged $953 per ounce sold in Q3 2024, an increase from $794 in Q3 2023, and $939 the nine months ended September 30, 2024 from $858 in the nine months ended September 30, 2023. The increases in both the three and nine-month periods were primarily due to higher royalties (driven by higher gold prices) and labour costs.
In the quarter, AISC4 averaged $1,335 per ounce sold in Q3 2024, an increase from $1,177 in Q3 2023, and $1,310 the nine months ended September 30, 2024 from $1,225 in the nine months ended September 30, 2023, with the increases in both the three and nine-month periods due to higher total cash costs combined with higher sustaining capital.
Eldorado reported net earnings attributable to shareholders from continuing operations of $101.1 million ($0.49 earnings per share) in Q3 2024 compared to a net loss of $6.6 million ($0.03 loss per share) in Q3 2023 and net earnings of $192.7 million ($0.95 earnings per share) in the nine months ended September 30, 2024 compared to net earnings of $14.4 million ($0.07 earnings per share) in the nine months ended September 30, 2023. The increases in net earnings in both the three and nine-month periods were driven by higher operating income due primarily to higher average realized gold price as well as stronger gold sales and the gain on deferred consideration, partially offset by higher unrealized derivative losses.
Adjusted net earnings4 was $71.0 million ($0.35 earnings per share) in Q3 2024 compared to adjusted net earnings of $35.0 million ($0.17 earnings per share) in Q3 2023. Adjustments in Q3 2024 include a $33.1 million unrealized loss on derivative instruments, a $50.1 million gain on recognition of deferred consideration net of tax impacts related to commercial production being declared at the Tocantinzinho Mine, which was divested to G Mining Ventures in 2021, and a $15.3 million gain on foreign exchange due to the translation of deferred tax balances and Turkiye inflation accounting.
Adjusted net earnings was $192.9 million ($0.95 earnings per share) in the nine months ended September 30, 2024 compared to adjusted net earnings of $61.4 million ($0.32 earnings per share) in the nine months ended September 30, 2023. Adjustments in the nine months ended September 30, 2024 include a $61.9 million unrealized loss on derivative instruments, a $50.1 million gain on recognition of deferred consideration net of tax impacts mentioned above, and a $11.9 million gain on foreign exchange due to the translation of deferred tax balances net of Turkiye inflation accounting.
Quarterly Operations Update
3 months ended September 30, | 9 months ended September 30, | ||||||||||||
2024 | 2023 | 2024 | 2023 | ||||||||||
Consolidated | |||||||||||||
Ounces produced | 125,195 | 121,030 | 364,625 | 341,973 | |||||||||
Ounces sold | 123,828 | 119,200 | 361,062 | 339,151 | |||||||||
Production costs | $141.2 | $115.5 | $392.0 | $341.3 | |||||||||
Total cash costs ($/oz sold) (1,2) | $953 | $794 | $939 | $858 | |||||||||
All-in sustaining costs ($/oz sold) (1,2) | $1,335 | $1,177 | $1,310 | $1,225 | |||||||||
Sustaining capital expenditures (2) | $33.3 | $31.8 | $93.2 | $83.9 | |||||||||
Kisladag | |||||||||||||
Ounces produced | 41,084 | 37,219 | 117,597 | 108,558 | |||||||||
Ounces sold | 40,724 | 38,732 | 117,068 | 108,405 | |||||||||
Production costs | $37.3 | $28.6 | $106.5 | $86.7 | |||||||||
Total cash costs ($/oz sold) (1,2) | $899 | $722 | $889 | $778 | |||||||||
All-in sustaining costs ($/oz sold) (1,2) | $1,028 | $884 | $1,002 | $897 | |||||||||
Sustaining capital expenditures (2) | $3.7 | $5.5 | $8.9 | $10.5 | |||||||||
Lamaque | |||||||||||||
Ounces produced | 43,106 | 43,821 | 132,796 | 120,450 | |||||||||
Ounces sold | 44,531 | 40,908 | 132,776 | 119,455 | |||||||||
Production costs | $32.8 | $26.9 | $101.6 | $84.4 | |||||||||
Total cash costs ($/oz sold) (1,2) | $728 | $648 | $755 | $697 | |||||||||
All-in sustaining costs ($/oz sold) (1,2) | $1,189 | $1,099 | $1,228 | $1,143 | |||||||||
Sustaining capital expenditures (2) | $20.0 | $18.0 | $61.1 | $52.0 | |||||||||
Efemcukuru | |||||||||||||
Ounces produced | 19,794 | 21,142 | 60,692 | 63,714 | |||||||||
Ounces sold | 19,741 | 21,364 | 60,817 | 63,581 | |||||||||
Production costs | $26.4 | $20.6 | $73.0 | $58.7 | |||||||||
Total cash costs ($/oz sold) (1,2) | $1,325 | $990 | $1,185 | $947 | |||||||||
All-in sustaining costs ($/oz sold) (1,2) | $1,578 | $1,205 | $1,336 | $1,137 | |||||||||
Sustaining capital expenditures (2) | $4.7 | $3.7 | $10.7 | $9.6 | |||||||||
Olympias | |||||||||||||
Ounces produced | 21,211 | 18,848 | 53,540 | 49,251 | |||||||||
Ounces sold | 18,833 | 18,196 | 50,401 | 47,710 | |||||||||
Production costs | $44.7 | $39.3 | $110.9 | $111.6 | |||||||||
Total cash costs ($/oz sold) (1,2) | $1,210 | $1,048 | $1,241 | $1,325 | |||||||||
All-in sustaining costs ($/oz sold) (1,2) | $1,513 | $1,319 | $1,520 | $1,614 | |||||||||
Sustaining capital expenditures (2) | $4.9 | $4.7 | $12.5 | $11.8 |
(1) | Revenues from silver, lead and zinc sales are off-set against total cash costs. | |
(2) | These financial measures or ratios are non-IFRS financial measures or ratios. See the section ‘Non-IFRS and Other Financial Measures and Ratios’ of our MD&A for explanations and discussions of these non-IFRS financial measures or ratios. | |
Kisladag
Kisladag produced 41,084 ounces of gold in Q3 2024, a 10% increase from 37,219 ounces produced in Q3 2023. Production in the quarter benefited from both higher average grade and higher stacking rates from earlier in the year. Grade slightly increased from 0.85 grams per tonne in Q3 2023 to 0.86 grams per tonne in Q3 2024 as a result of mine planning changes and positive grade reconciliation.
Availability of the crushing circuit has been impacted due to maintenance issues, leading to slightly lower tonnes stacked compared to plan. We are working on a solution and expect to install it in Q1 2025. In addition, a small portion of the ore product coming from the high pressure grinding rolls contains particles that are greater than 10mm which has slightly reduced recovery due to the larger particle size. As we continue to analyze data following the ramp-up of the HPGR and agglomeration drum, we are seeing leach cycles extending beyond the planned 220 days which leads to an increase in gold inventory.
We have responded to these operational challenges through irrigation optimization activities, which have demonstrated positive results through the drawdown of gold inventory partially offsetting the longer leach cycle. Additionally, as we have previously discussed, a geometallurgical study has commenced with drilling currently underway. Starting in Q4 2024, as the new Adsorption-Desorption facility goes into operations we will also realize a number of benefits at Kisladag including: reducing carbon handling requirements, realigning the extraction cycle with the stacking cycle and decoupling the North and South heap leach facilities.
Revenue increased to $102.2 million in Q3 2024 from $75.2 million in Q3 2023, reflecting the higher average realized gold price as well as higher ounces sold.
Production costs increased to $37.3 million in Q3 2024 from $28.6 million in Q3 2023, with more than half the increase attributable to the higher sales volume, as well as higher royalty expense due to both the higher average realized gold price and higher gold sales. As a result, total cash costs per ounce increased to $899 in Q3 2024 from $722 in Q3 2023.
AISC per ounce sold increased to $1,028 in Q3 2024 from $884 in Q3 2023, primarily due to the increase in total cash costs per ounce sold.
Sustaining capital expenditures were $3.7 million in Q3 2024 and $8.9 million in the nine months ended September 30, 2024, which primarily included equipment rebuilds, mine equipment purchases and geotechnical drilling and monitoring. Growth capital investment of $27.4 million and $85.1 million in the three and nine months ended September 30, 2024 and was primarily related to waste stripping and associated equipment costs to support the mine life extension, continued construction of the second phase of the North Heap Leach Pad and adsorption-desorption-regeneration plant infrastructure, and preparation work for building relocation due to pit expansion.
Lamaque
Lamaque produced 43,106 ounces of gold in Q3 2024, compared to 43,821 ounces in Q3 2023. The slight decrease was primarily due to lower grades processed, partially offset by increased throughput. Average grade decreased to 6.03 grams per tonne in Q3 2024 from 7.04 grams per tonne in the comparative quarter.
Revenue increased to $111.6 million in Q3 2024 from $79.1 million in Q3 2023, reflecting the higher average realized gold price as well as higher ounces sold.
Production costs increased to $32.8 million in Q3 2024 from $26.9 million in Q3 2023 due to higher sales volume, as well as additional costs incurred in labour, contractors, and equipment rentals. Total cash costs were also impacted by slightly higher royalties due to the higher average realized gold price, with total cash costs per ounce sold increasing to $728 in Q3 2024 from $648 in Q3 2023.
AISC per ounce sold increased to $1,189 in Q3 2024 from $1,099 in Q3 2023, primarily due to higher total cash costs per ounce as well as higher sustaining capital.
Sustaining capital expenditures of $20.0 million in Q3 2024 and $61.1 million in the nine months ended September 30, 2024 primarily included underground development, equipment rebuilds and expenditure on the expansion of the tailings facility. Growth capital investment of $6.4 million in Q3 2024 and $18.9 million in the nine months ended September 30, 2024 was primarily related to resource conversion drilling and initiation of the bulk sample development at Ormaque.
The inaugural reserve at Ormaque is expected to be announced by the end of 2024, and material for the bulk sample is now being stockpiled in preparation for processing through the mill in December.
Efemcukuru
Efemcukuru produced 19,794 ounces of gold in Q3 2024, a 6% decrease from 21,142 ounces in Q3 2023. The slight decrease was primarily driven by lower throughput and lower grade.
Revenue increased to $52.3 million in Q3 2024 from $39.1 million in Q3 2023, with the increase attributable to the higher average realized gold price, partially offset by lower sales volume.
Production costs increased to $26.4 million in Q3 2024 from $20.6 million in Q3 2023, with the increase attributable to higher unit costs, primarily a result of increased royalty expense due to the higher average realized gold price during the quarter. Additionally, labour and transportation costs have increased compared to the comparative period of the prior year. Overall, this resulted in an increase to total cash costs per ounce sold to $1,325 in Q3 2024 from $990 in Q3 2023.
AISC per ounce sold increased to $1,578 in Q3 2024 from $1,205 in Q3 2023, primarily due to higher total cash costs per ounce.
Sustaining capital expenditures of $4.7 million in Q3 2024 and $10.7 million in the nine months ended September 30, 2024 were primarily related to underground development and equipment rebuilds. Growth capital investment of $1.2 million in Q3 2024 and $3.3 million in the nine months ended September 30, 2024 supported underground development to Kokarpinar.
Olympias
Olympias produced 21,211 ounces of gold in Q3 2024, a 13% increase from 18,848 ounces in Q3 2023 primarily driven by higher grade ore, which reflected stope sequencing in the quarter.
Revenue increased to $65.7 million in Q3 2024 from $51.4 million in Q3 2023, primarily as a result of the higher average realized gold price and slightly higher ounces sold.
Production costs increased to $44.7 million in Q3 2024 from $39.3 million in Q3 2023 driven by higher labour costs and higher royalty expenses as a result of higher realized gold prices, as well as higher gold ounces sold. The increase in unit costs, which were partially offset by higher by-product revenues, resulted in an increase to total cash costs per ounce sold to $1,210 in Q3 2024 from $1,048 in Q3 2023.
AISC per ounce sold increased to $1,513 in Q3 2024 from $1,319 in Q3 2023 primarily due to higher total cash costs per ounce sold.
Sustaining capital expenditures of $4.9 million in Q3 2024 and $12.5 million in the nine months ended September 30, 2024 primarily included underground development and process improvements. Growth capital investment of $4.1 million in Q3 2024 and $6.7 million in the nine months ended September 30, 2024 was primarily related to underground development and investment towards the mill throughput expansion.
During Q3 2024, the Collective Bargaining Agreement was finalized. This three-year agreement, combined with increased productivity in our underground operations and as contemplated in our guidance, supports the 650ktpa expansion, an increase from 500ktpa.
For further information on the Company’s operating results for the third quarter of 2024, please see the Company’s MD&A filed on SEDAR+ at www.sedarplus.com under the Company’s profile.
About Eldorado
Eldorado is a gold and base metals producer with mining, development and exploration operations in Turkiye, Canada and Greece. The Company has a highly skilled and dedicated workforce, safe and responsible operations, a portfolio of high-quality assets, and long-term partnerships with local communities. Eldorado’s common shares trade on the Toronto Stock Exchange and the New York Stock Exchange.
Scottie Resources Corp. (TSX-V: SCOT) (OTCQB: SCTSF) (FSE: SR80)... READ MORE
Denison Mines Corp. (TSX: DML) (NYSE AMERICAN: DNN) is pleased to... READ MORE
Baselode Energy Corp. (TSX-V: FIND) is pleased to announce the cl... READ MORE
Innovation Mining Inc. is pleased to announce outstanding metallu... READ MORE
Osisko Development Corp. (NYSE: ODV) (TSX-V: ODV) is pleased to announce... READ MORE