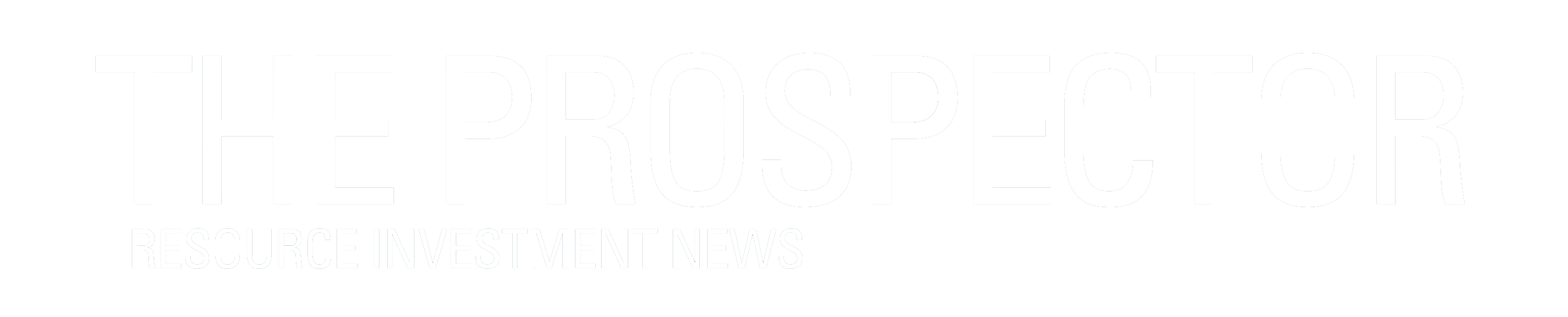
by Richard Roberts, Editorial Director, Beacon Events
Alan Young says the mining industry has had a happy knack of fighting disruptive change, losing the battle convincingly, and emerging in much better shape. On this basis, he says, capitulation on circularity should happen now so the industry collects another windfall as it advances back to Go.
The co-founder of Canada’s Materials Efficiency Research Group and veteran industry and government adviser says miners around the world resisted safety reforms and were at war with environmentalists for decades.
“We lost and we’re better for it,” Young said at the IMARC 2024 conference in Sydney, Australia.
“We’ve created considerable efficiencies and much better relationships internally [and externally].
“The good news about [circular economy and environmental systems] is it’s not just cost savings but it’s value realisation and a whole level of social partnership that is going to consolidate the industry’s role in the future.
“Some companies see it coming and see it as part of their business solution.
“Others are wishing it would go away and realising it probably won’t.
“But if you want to future proof your company and your industry you start to realise this is a fight you want to lose because if you won you’d be poorer for it.”
Young was joined on an IMARC panel focusing on the role of mining and metals in a circular economy by the founder of the Centre Innovation and Circular Economy in Chile, Petar Ostojic, and chief strategy officer at Australian Stock Exchange-listed mining technology and products company, Imdex, Dr Michelle Carey. The former is recognised by the World Economic Forum as “the first promoter of the circular economy in Latin America”.
“We’re living a paradigm shift, the fourth industrial revolution,” Ostojic told IMARC 2024.
“We think the economic model of this new revolution will be the circular economy.
“We always say [though], circularity is inevitable, but it’s not imminent.”
Imdex has assembled a technology stack that helps miners better characterise ore and waste before, during and after mining. Carey said early characterisation was the first step towards optimising the use of materials. “Sadly it is not something that we necessarily do particularly well and not because we can’t. There’s no shortage of technologies that allow things like that to happen. It’s more around people thinking through the full economic benefit and about the optionality that gets unlocked by truly characterising in the first place.”
US-based Clareo chair Peter Bryant chaired the panel, which proffered that the global mining and metals industry didn’t just have a role to play in a regenerative economic system, but that its part could and should be central.
“The beauty of minerals is that they’re the perfect circular substance,” said Young.
“You know, ultimately durable. The more you go through them the less it costs to process them, in most cases, assuming you’re not bending them into alloys.
“So unlike plastics, unlike agriculture, there’s a long term economic play that, in some cases, may lead to leasing mineral values instead of purchasing them or selling them.
“But more importantly, the long term minerals economy in circularity will run in perpetuity and the math on that is much more compelling than anything in agriculture or plastics.
“So on the one hand we need to work together to realise this at a more effective local and global level. On the other hand we’ve got a much better business case to start with.”
A more comprehensive case has been made in aluminium. Alcoa CEO Bill Oplinger told IMARC 2024, “something like 75% of all the aluminium made in history is still in use today because of the ability to recycle … So you’ve got that circular economy almost built into the economics of the industry.”
Significant parts of that value chain remain the focus of concerted work to cut waste and increase resource re-use.
Bryant provided a counterview with copper.
“Anything between five to seven million tonnes of copper, pre-consumer waste and post-consumer, is not recycled,” he said.
“That’s billions of dollars in annual economic opportunity. Yet nothing’s happening.
“And the rate of capture is not increasing much.
“If no one is moving on that then why would they move on waste and all the other stuff?”
Young agreed public policy was a barrier in many countries and economic incentives were clearly not properly aligned, though, he said, much of this came down to “bad accounting”.
“One of the problems the industry faces is it is hamstrung by policy that was set on a waste management model that is 20th century, to be generous, but often impedes the ability to use waste and transport that waste in a way that could treat it as a resource,” he said.
“So we do have some handcuffs on existing policy that really need to be rethought.
“But [miners] are leaving billions of dollars on the table that could well be in their coffers and [those of] their partners.
“We only do that because of bad accounting.
“We’re moving from sustainability as a high-cost hirsute to circularity as a profound potential business growth area and not just for the mining companies themselves.
“One of the distinguishing factors in the circular economy is the integration throughout supply chains – the partnerships through supply chains to close loops and create efficiencies.
“And the good news is that the pressure from downstream sectors – electronics, automotive, green energy and in the finance community – is really driving this.
“They’re sending the signals that we want verifiable, responsible sourcing of minerals, but that they become a partner in that.
“So the good news about the opportunities around collaboration and coordination is that it shares the burden and it also shares the benefits in a much more stable way over time.
“That creates stability … that partnership brings more resources to the table which then encourage innovation.
“Arguably one of the problems we’ve had with the ESG movement so far is it’s lacked that coordination. It’s lacked that collaboration. One end [of the supply chain] is asking for something in a very imprecise and often unhelpful way. By bringing these together we can do much more targeted investments in responsible sourcing in a variety of ways so that we know from the beginning to the end, through data, through policy and through markets, that we’re getting what we ask for and we’re producing what is being asked for.
“And this shared benefit, shared burden model … is going to end up on the right side of the ledger, I’m absolutely convinced of that.”
Young told Mining Beacon his “bad accounting” assessment was made through a circular economy lens.
“Traditionally mining is an industry predicated on the need to create millions of tonnes of waste of various kinds in order to access the minute, high-value objective,” he said, highlighting typical 0.6-0.8% average copper ore grades currently being mined worldwide (depending on your source).
“Needless to say the final products that emerge from these production systems are often dwarfed by the vast quantities of resource inputs that ultimately are treated as waste.
“So the reality is that the majority of a mining companies’ actual business is managing all of the other resource inputs that it takes to make that high value by-product.
“This reality suggests that there needs to be a very careful and creative approach to how all these waste materials are being used, transformed or disposed of in order to minimise liabilities – current and future – and to identify where a waste can be re-purposed as a resource, either onsite or offsite with upstream or downstream partners.
“This kind of systematic analysis and inventorying of waste-to-resource stocks and opportunities is very rarely done and is at the heart of the transition to a circular economy approach.”
On evidence he had seen even the most sophisticated and “profitable” companies were neglecting these types of analyses, let alone implementation.
It was “shockingly absent or piecemeal at best”.
“On the upside it has been demonstrated that the management and reuse of tailings, which are often hazardous, can yield significant reductions in costs and liabilities while in some cases yielding resource streams from elements discarded in the primary extraction processes,” he said.
“Additionally, it is possible to use [circular economy] strategies to reduce the consumption of water, machinery, tyres, and chemicals within mining operations to significantly reduce resource use and waste, ultimately leading to improved end-of-life management of products and also processes that generate substantial structural waste.
“Tyres are often used as an example of structural waste given how much they play a role in openpit mining in particular.
“I have read that an average large-scale mine in Chile uses around 3000 tonnes of tyres annually.
“Historically these would have been landfilled back in the pit or elsewhere, but increasingly they are being resold as feedstock for a variety of downstream purposes.”
Ostojic also highlighted during the conference industrial pump recycling applications.
“There are many more, including the very important use of tailings sands for regional and municipal infrastructure issues, the use of municipal wastewater for mineral processing and the investment in shared water and other infrastructure to avoid costly regional and industrial duplication,” Young said.
“There are so many other ways that costs can be reduced, shared or eliminated by designing for deconstruction.
“However, companies and suppliers are not sufficiently empowered to implement these kinds of innovative CE practices.”
“Bad accounting” also partly referred to bureaucratic challenges and a mining industry business model that hindered innovation internally and with external suppliers and potential partners, Young said.
“Administrative hurdles mining companies impose make it difficult for suppliers to retain and repurpose materials,” he said.
“The ledger books account for these kinds of issues and materials with a linear waste model that has internalised the costs and liabilities of low-value scrap and waste.
“There are innumerable examples of broken, discarded, unused or underused materials simply being written off.
“If we are lucky these end up in some form of stabilised waste pile. But as we know, whether it is in terms of structural or geo-chemical issues, this is not always done safely and these liabilities are rarely truly accounted for by governments or companies.
“And if you consider the increasing scarcity of water or land itself these kinds of low-value waste disposal strategies are becoming increasing untenable.
“If the accounting was to be done differently, with a view to designing waste out of the systems rather than accepting waste as a core by-product of the system, each instance of waste would be inventoried and evaluated for alternative resource options and systems.
“Mine sites would look very, very different, and so would their accounts.”
Innovation Mining Inc. is pleased to announce outstanding metallu... READ MORE
Osisko Development Corp. (NYSE: ODV) (TSX-V: ODV) is pleased to announce... READ MORE
Cascadia Minerals Ltd. (TSX-V:CAM) (OTCQB:CAMNF) is pleased to an... READ MORE
Kuya Silver Corporation (CSE: KUYA) (OTCQB: KUYAF) (FSE: 6MR1) an... READ MORE
Blue Sky Uranium Corp. (TSX-V: BSK) (FSE: MAL2) (OTC: BKUCF) anno... READ MORE