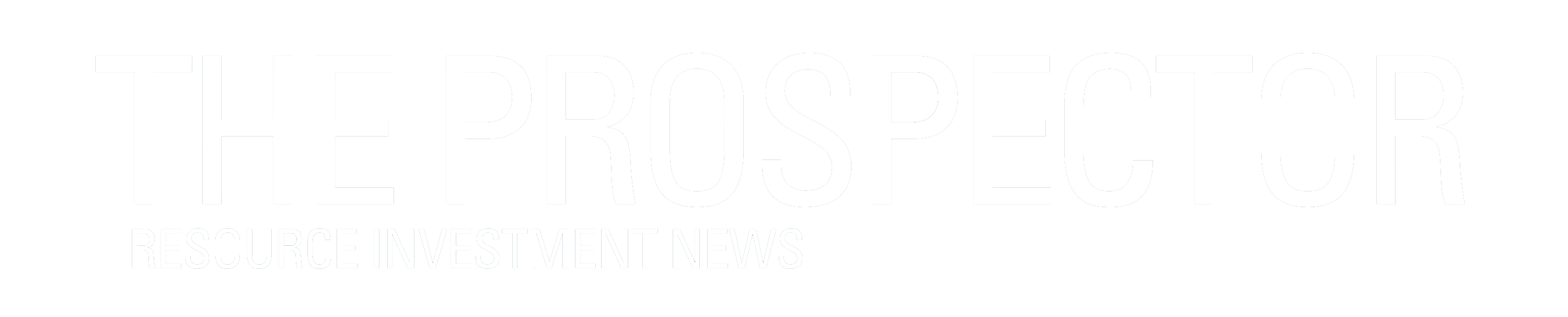
Record quarterly production of 2.9M wmt, adjusted EPS1 of $0.06 and EBITDA1 of $84.3 million; Bloom Lake Phase II expansion ramping-up as scheduled, contributing towards reducing operating costs metrics; Declares a dividend of $0.10 per ordinary share
Champion Iron Limited (TSX: CIA) (ASX: CIA) (OTCQX: CIAFF) is pleased to announce operational and financial results for the financial second quarter ended September 30, 2022.
Champion’s CEO, Mr. David Cataford, said: “Our record production is attributable to the hard work and dedication of our team as Phase II continues to ramp-up as scheduled, despite the challenging environment. As a result, our iron ore volumes sold in the quarter increased by nearly 43% year on year. With Phase II on track to reach commercial production by the end of the calendar year, the higher production volumes are also contributing towards normalizing our operating costs per tonne sold. In addition, our team is finalizing the feasibility study evaluating the production of a Direct Reduction pellet feed product, which will be the foundation towards our potential transition to higher value products in the green steel supply chain.”
Sustainability
Operations and Financial
Phase II Milestones
Growth and Development
Three Months Ended | Six Months Ended | |||||||
September 30, | September 30, | |||||||
2022 | 2021 | Variance | 2022 | 2021 | Variance | |||
Operating Data | ||||||||
Waste mined and hauled (wmt) | 4,572,900 | 5,299,600 | (14 %) | 10,178,900 | 9,999,100 | 2 % | ||
Ore mined and hauled (wmt) | 8,214,700 | 5,713,900 | 44 % | 14,407,800 | 11,357,800 | 27 % | ||
Material mined and hauled (wmt) | 12,787,600 | 11,013,500 | 16 % | 24,586,700 | 21,356,900 | 15 % | ||
Strip ratio | 0.56 | 0.93 | (40 %) | 0.71 | 0.88 | (19 %) | ||
Ore milled (wmt) | 8,102,700 | 5,679,800 | 43 % | 14,124,900 | 10,907,000 | 30 % | ||
Head grade Fe (%) | 29.5 | 29.1 | 1 % | 30.2 | 29.4 | 3 % | ||
Fe recovery (%) | 78.6 | 83.3 | (6 %) | 79.3 | 83.1 | (5 %) | ||
Product Fe (%) | 66.1 | 66.3 | — % | 66.1 | 66.3 | — % | ||
Iron ore concentrate produced (wmt) | 2,857,300 | 2,089,100 | 37 % | 5,139,900 | 4,025,100 | 28 % | ||
Iron ore concentrate sold (dmt) | 2,793,400 | 1,953,900 | 43 % | 4,807,300 | 3,928,600 | 22 % |
Phase II Commissioning
During the first quarter of the 2023 financial year, the Company initiated and advanced the commissioning of Phase II and at the end of April 2022, the first of two Phase II plant production lines was commissioned. The first shipments were railed on May 3, 2022. In June 2022, the Company successfully started the second line as scheduled in the ramp-up sequencing of the project. Accordingly, both operating lines were in service at the end of the first quarter. During the three-month period ended September 30, 2022, commissioning activities progressed as scheduled. The Company made adjustments and improvements in some areas to stabilize operations (including work to increase throughput and the recovery ratio) and reach expected performance, positioning the Company to achieve, as scheduled, commercial production by the end of calendar 20223 and nameplate capacity in calendar 20233. The last major on-site work program relating to the Phase II equipment was completed during the three-month period ended September 30, 2022, enabling the Company’s two crushers to feed both facilities and reduce bottlenecks during maintenance periods. Final minor on-site work programs are expected to be completed as planned during the third and fourth quarters of the 2023 financial year. While on-site work programs are being delivered ahead of schedule, off-site work programs, including third-party infrastructure, continue to advance as scheduled.
Operational Performance
Second Quarter of the 2023 Financial Year vs Second Quarter of the 2022 Financial Year
In the three-month period ended September 30, 2022, 12.8 million tonnes of material were mined and hauled, compared to 11.0 million tonnes during the same period in 2021, an increase of 16%. The increase in material movement was enabled through the utilization of additional equipment compared to the same prior-year period, offset by a longer haul cycle as material was sourced from different pits, including those that deepened with mining activities over time. The lower strip ratio for the three-month period ended September 30, 2022, is in line with the revised mine plan in connection with transitional incremental feed requirements during the Phase II ramp-up period.
The iron ore head grade for the three-month period ended September 30, 2022, was 29.5%, compared to 29.1% for the same period in 2021. The variation in head grade is attributable to the presence of some higher-grade ore being sourced and blended from different pits, which was anticipated and is in line with the mine plan and the LoM head grade average.
The Company’s average Fe recovery rate for the three-month period ended September 30, 2022, was negatively impacted by the anticipated lower recoveries during the commissioning of the Phase II concentrator, but is in line with Management’s expectations at this stage of the Phase II commissioning. The slight decrease in the Fe recovery rate during the three-month period ended September 30, 2022, compared to the first quarter, was due to a higher proportion of tonnes processed by the second concentrator together with stability impacts on Phase I attributable to the finalization of the Phase II tie-in program, as the utilization of the second plant is increasing over time. The Company expects to reach a stable Fe recovery circuit when Phase II achieves commercial production, anticipated to occur by the end of calendar 20223.
During the three-month period ended September 30, 2022, operational activities were impacted by a scheduled semi-annual maintenance on the second concentrator, while no shutdown occurred in the same prior-year period. A shutdown is now planned every quarter, alternating between the two concentrators and related facilities. A non-recurring 20-day scheduled shutdown of specific equipment was required for the tie-in of the first crusher to the A-Frame dome as part of the Phase II project ramp-up, which also impacted operational activities in the quarter. Despite these factors, Bloom Lake produced 2.9 million wmt of high-grade iron ore concentrate during the three-month period ended September 30, 2022, an increase of 37%, compared to 2.1 million wmt during the same period in 2021. The Company achieved record production in connection with the commissioning of the second plant at the mine site. Higher throughput and head grade also contributed to higher production volumes, despite a lower global recovery. The commissioned Phase II project’s production compares favourably to the scheduled production volumes. The plants processed 8.1 million tonnes of ore during the three-month period ended September 30, 2022, compared to 5.7 million tonnes for the same prior-year period. The throughput for the period was positively affected by higher availability of mined ore and the commissioning of Phase II operations in the previous quarters.
First Six Months of the 2023 Financial Year vs First Six Months of the 2022 Financial Year
The Company mined and hauled 24.6 million tonnes of material during the six-month period ended September 30, 2022, compared to 21.4 million tonnes for the same period in 2021. This increase in material mined and hauled is attributable to the commissioning of additional operational equipment compared to the same prior-year period. The strip ratio was 0.71 for the six-month period ended September 30, 2022, compared to 0.88 for the same period in 2021, and is consistent with the revised mine plan.
The iron ore head grade of 30.2% for the six-month period ended September 30, 2022, was attributable to different sourcing pits, compared to 29.4% for the same period in 2021, and is consistent with the LoM head grade average. The lower average Fe recovery rate for the six-month period ended September 30, 2022, was attributable to the commissioning of the Phase II concentrator as detailed above.
The plant processed 14.1 million tonnes of ore during the six-month period ended September 30, 2022, an increase of 30% over the same period in 2021, and produced 5.1 million wmt of high-grade iron ore concentrate, compared to 4.0 million wmt for the same period in 2021, mainly attributable to the commissioning of the Phase II project.
Three Months Ended | Six Months Ended | |||||||
September 30, | September 30, | |||||||
2022 | 2021 | Variance | 2022 | 2021 | Variance | |||
Financial Data (in thousands of dollars) | ||||||||
Revenues | 300,621 | 331,006 | (9 %) | 579,942 | 876,414 | (34 %) | ||
Cost of sales | 199,841 | 110,884 | 80 % | 369,248 | 231,730 | 59 % | ||
Other expenses | 16,839 | 20,313 | (17 %) | 32,444 | 34,873 | (7 %) | ||
Net finance costs | 10,765 | 1,012 | 964 % | 14,955 | 5,399 | 177 % | ||
Net income | 19,530 | 114,596 | (83 %) | 61,084 | 338,935 | (82 %) | ||
EBITDA1 | 84,331 | 200,013 | (58 %) | 179,261 | 605,752 | (70 %) | ||
Statistics (in dollars per dmt sold) | ||||||||
Gross average realized selling price1 | 157.0 | 218.8 | (28 %) | 171.0 | 249.4 | (31 %) | ||
Net average realized selling price1 | 107.6 | 169.4 | (36 %) | 120.6 | 223.1 | (46 %) | ||
C1 cash cost1 | 65.9 | 56.2 | 17 % | 69.3 | 58.2 | 19 % | ||
All-in sustaining cost (“AISC”)1 | 81.9 | 73.6 | 11 % | 86.8 | 73.1 | 19 % | ||
Cash operating margin1 | 25.7 | 95.8 | (73 %) | 33.8 | 150.0 | (77 %) |
Second Quarter of the 2023 Financial Year vs Second Quarter of the 2022 Financial Year
During the three-month period ended September 30, 2022, 2.8 million tonnes of high-grade iron ore concentrate were sold at a gross average realized price1 of US$120.6/dmt, before freight and other costs and provisional pricing adjustments, compared to US$174.6/dmt for the same prior-year period. The decrease in gross average realized selling price1 reflects lower index prices during the three-month period ended September 30, 2022, compared to the same prior-year period. Despite lower index prices, the gross average realized selling price1 of US$120.6/dmt represents a premium of 16.7% over the benchmark IODEX 62% Fe CFR China Index (“P62”) price for the period, compared to a premium of 7.2% for the same period in 2021.
During the three-month period ended September 30, 2022, the IODEX 65% Fe CFR China Index (“P65”) for high-grade iron ore fluctuated from a high of US$131.5/dmt to a low of US$107.2/dmt. The P65 index average price for the period was US$115.5/dmt, a decrease of 39% from the same prior-year quarter, resulting in an average premium of 11.8% over the P62 reference price of US$103.3/dmt. The gross average realized selling price1 of US$120.6/dmt was higher than the P65 index average price for the period of US$115.5/dmt due to sales based on fixed backward-looking iron ore prices, when prices were higher compared to the P65 index average for the current period. This factor was partially offset by the negative impact of 1.3 million tonnes which were in transit as at September 30, 2022, provisionally priced using an average forward price of US$112.3/dmt, which was lower than the P65 index average price for the period. After accounting for sea freight and other costs and provisional pricing adjustments, the Company’s net realized FOB selling price1 was US$83.2/dmt, compared to US$134.7/dmt for the same period in 2021.
The average C3 Baltic Capesize Index for the three-month period ended September 30, 2022, was US$24.0/t compared to US$31.7/t for the same period in 2021, representing a decrease of 24%, which contributed to lower freight costs in the three-month period ended September 30, 2022, compared to the same prior-year period. The lower freight rates for the three-month period ended September 30, 2022, can be partially attributed to decreased fuel prices and lower iron ore shipments from Brazil. Simultaneously, the partial removal of COVID-19 lockdowns in China reduced port congestion, further influencing the decreasing freight rates, with lower seaborn iron ore volumes as marginal suppliers facing profitability challenges curtailed operations. Champion typically contracts vessels three to four weeks prior to the desired laycan period. This creates a natural delay between the freight paid and the C3 route index price. The effects of these delays are eventually reconciled since the Company ships its high-grade iron ore concentrate uniformly throughout the year.
Provisional pricing adjustments on previous sales, which were directly correlated to the decrease in the P65 index during the quarter, contributed to decreasing the net average realized selling price1. During the three-month period ended September 30, 2022, a final price of US$116.2/dmt was established for the 0.7 million tonnes of iron ore that were in transit as at June 30, 2022, and which were previously evaluated using an average expected price of US$138.4/dmt. Accordingly, during the three-month period ended September 30, 2022, net negative provisional pricing adjustments of $20.9 million were recorded as a decrease in revenues for the 0.7 million tonnes, representing a negative impact of US$5.3/dmt over the total volume of 2.8 million dmt sold during the current period, comparable to the negative impact for the same period in 2021.
After taking into account sea freight and other costs of US$32.1/dmt and the negative provisional pricing adjustment of US$5.3/dmt, the Company obtained a net average realized selling price1 of US$83.2/dmt (CA$107.6/dmt) for its high-grade iron ore delivered to the end customer. Revenues totalled $300.6 million for the three-month period ended September 30, 2022, compared to $331.0 million for the same period in 2021, reflecting the lower net average realized selling price1 partially offset by a significantly higher sales volume and the weakening Canadian dollar.
First Six Months of the 2023 Financial Year vs First Six Months of the 2022 Financial Year
For the six-month period ended September 30, 2022, the Company sold 4.8 million tonnes of iron ore concentrate, mainly to customers in China, Japan, South Korea and Europe. While the high-grade iron ore P65 index price fluctuated between a low of US$107.2/dmt and a high of US$185/dmt during the six-month period ended September 30, 2022, the Company sold its product at a gross average realized selling price1 of US$132.7/dmt before sea freight and other costs and provisional pricing adjustments. The P65 index average price for the six-month period ended September 30, 2022, was US$137.3/dmt, a decrease of 35% from the same period in 2021, resulting in an average premium of 14.2% over the P62 index reference price of US$120.2/dmt. The gross average realized selling price1 is lower than the average P65 high-grade index of US$137.3/dmt for the period due to sales provisionally priced using an average forward price of US$112.3/dmt at the end of the period, which was significantly lower than the average P65 index for the period. The Company expects its iron ore concentrate pricing to track the P65 index in the long term.
Combining the gross average realized selling price1 with the negative provisional pricing adjustment of US$5.8/dmt, the Company sold its high-grade iron ore at a price of US$126.9/dmt during the six-month period ended September 30, 2022, compared to the P65 high-grade index average of US$137.3/dmt. Deducting sea freight and other costs of US$33.1/dmt, the Company obtained a net average realized selling price1 of US$93.8/dmt (CA$120.6/dmt) for its high-grade iron ore. As such, revenues totalled $579.9 million for the six-month period ended September 30, 2022, compared to $876.4 million for the same period in 2021, mainly as a result of a lower gross average realized selling price1, partially offset by a significantly higher sales volume and the weakening Canadian dollar. A negative provisional pricing adjustment during the six-month period ended September 30, 2022, compared to a positive provisional pricing adjustment during the same period in 2021, also contributed to the decrease in revenues.
The cost of sales represents mining, processing, and mine site-related general and G&A expenses as well as rail and port operation costs. It also includes specific and incremental costs related to COVID-19 and, starting in April 2022, it includes Bloom Lake Phase II start-up costs incurred after commissioning. These start-up costs mainly include abnormal operational costs attributable to the facility not having reached the normalized expected level of output.
For the three-month period ended September 30, 2022, the cost of sales totalled $199.8 million, compared to $110.9 million for the same period in 2021. During the three-month period ended September 30, 2022, the C1 cash cost1 per tonne, excluding specific and incremental costs related to COVID-19 and Phase II start-up costs, totalled $65.9/dmt, compared to $56.2/dmt for the same period in 2021.
The C1 cash cost1 per dmt sold for the three-month period ended September 30, 2022, benefited from higher volumes of iron ore concentrate sold associated with increased production volumes from the Phase II project, but were more than fully offset by global inflationary pressures, impacting cost of fuel used in the Company’s mining activities and land transportation, explosives costs as well as rail and port operations. The life of mine stripping ratio used for cost capitalization for the three-month period ended September 30, 2021, was also significantly lower, positively impacting the prior-year period cash cost1. The lower recoveries associated with the commissioning of the Phase II concentrator also negatively impacted cash cost1 for the period as the concentrate volume produced was lower than standard level. Finally, longer haul cycle times associated with the current mine plan also contributes quarter-over-quarter to higher mining costs.
For the six-month period ended September 30, 2022, the Company produced high-grade iron ore at a C1 cash cost1 amounting to $69.3/dmt, compared to $58.2/dmt for the six-month period ended September 30, 2021. The variation is attributable to the same factors that affected the C1 cash cost1 for the three-month period ended September 30, 2022.
In addition, unplanned third-party shutdowns, planned maintenance of additional facilities, as well as increased headcount and subcontractor usage in relation to the commissioning of the Phase II project during the first quarter, also contributed to the higher cash cost1 for the six-month period ended September 30, 2022.
Second Quarter of the 2023 Financial Year vs Second Quarter of the 2022 Financial Year
For the three-month period ended September 30, 2022, the Company generated net income of $19.5 million (EPS of $0.04), compared to $114.6 million (EPS of $0.23) for the same period in 2021. The net income was mainly affected by a lower P65 index average price during the period, as well as a higher cash cost1, compared to the same prior-year period. The decrease in net income is partially offset by a higher sales volume driven by the solid ramp-up of Phase II and lower current income and mining taxes.
For the three-month period ended September 30, 2022, the Company generated EBITDA1 of $84.3 million, representing an EBITDA margin1 of 28%, compared to $200.0 million, representing an EBITDA margin1 of 60%, for the same period in 2021. The decrease in EBITDA1 period-over-period is primarily due to lower net average realized selling prices1 and higher cash costs1. This decrease is partially offset by a higher sales volume driven by the solid ramp-up of Phase II.
First Six Months of the 2023 Financial Year vs First Six Months of the 2022 Financial Year
For the six-month period ended September 30, 2022, the Company generated net income of $61.1 million (EPS of $0.12), compared to $338.9 million (EPS of $0.67) for the same period in 2021. The decrease in net income is mainly due to lower iron ore index prices and higher cash costs, partially offset by a higher sales volume driven by the solid commissioning of Phase II and lower current income and mining taxes.
For the six-month period ended September 30, 2022, the Company generated an EBITDA1 of $179.3 million, representing an EBITDA margin1 of 31%, compared to $605.8 million, representing an EBITDA margin1 of 69% for the same period in 2021. This decrease in EBITDA1 is mainly attributable to the decrease in the net average realized selling price1 and higher production costs, partially offset by a higher sales volume following the Phase II commissioning.
During the three-month period ended September 30, 2022, the Company realized an AISC1 of $81.9/dmt, compared to $73.6/dmt for the same period in 2021. The increase relates to higher C1 cash costs1, partially offset by the positive impact of higher volumes of iron ore concentrate sold.
The Company generated a cash operating margin1 of $25.7/dmt for each tonne of high-grade iron ore concentrate sold during the three-month period ended September 30, 2022, compared to $95.8/dmt for the same prior-year period. The variation is mainly due to a lower net average realized selling price1 and higher AISC1 for the period.
During the six-month period ended September 30, 2022, the Company recorded an AISC1 of $86.8/dmt, compared to $73.1/dmt for the same period in 2021. The variation is mainly due to higher C1 cash costs1 and higher sustaining capital expenditures mainly related to higher investments made in tailings lifts. The Company is actively working to ensure everything is in place to support Phase II operations, including hiring additional personnel and incurring the necessary sustaining capital expenditures. Refer to section 5 – Cash flow for details on sustaining capital expenditures.
The cash operating margin1 totalled $33.8/dmt for the six-month period ended September 30, 2022, compared to $150.0/dmt for the same period in 2021. The variation is mainly due to a lower net average realized selling price1 and higher AISC1.
During the three and six-month periods ended September 30, 2022, the Company maintained all of its properties in good standing and did not enter into any farm-in/farm-out arrangements. During the three and six-month periods ended September 30, 2022, $0.9 million and $3.1 million in exploration and evaluation expenditures were incurred, respectively, compared to $2.0 million and $2.7 million for the same periods in 2021. During the three and six-month periods ended September 30, 2022, exploration and evaluation expenditures mainly consisted of costs associated with resource development and drilling, work related to updating the Kami Project feasibility study and claim renewal fees. During the six-month period ended September 30, 2022, 4,430 metres of diamond drilling was completed on the Bloom Lake property. Drilling at Bloom Lake was undertaken mainly for the conversion of resources. Geological mapping and assessment were started on exploration claims localized south of Bloom Lake. In addition, late in September, the Company started a diamond drilling campaign at Lamêlée South.
Details on exploration projects and maps are available on the Company’s website at www.championiron.com under the section Operations & Projects.
Three Months Ended | Six Months Ended | |||||||
September 30, | September 30, | |||||||
2022 | 2021 | 2022 | 2021 | |||||
(in thousands of dollars) | ||||||||
Tailings lifts | 28,440 | 14,174 | 37,425 | 20,512 | ||||
Stripping and mining activities | 3,730 | 8,684 | 14,793 | 17,218 | ||||
Mining equipment rebuild | 4,011 | 3,603 | 10,908 | 5,498 | ||||
Sustaining capital expenditures | 36,181 | 26,461 | 63,126 | 43,228 | ||||
Other capital development expenditures at Bloom Lake | 42,403 | 127,192 | 138,072 | 220,364 | ||||
Purchase of property, plant and equipment as per cash flows | 78,584 | 153,653 | 201,198 | 263,592 |
Sustaining Capital Expenditures
The increase in tailings-related investments for the three and six-month periods ended September 30, 2022, is due to the reclassification of preparation work performed on Phase II dikes from other capital development expenditures in the comparative periods to tailings lifts. In addition, during the three and six-month periods ended September 30, 2022, weather conditions were more favourable than in the same prior-year periods, enabling the Company to advance work performed on the dikes. As part of the Company’s ongoing and thorough tailings infrastructure monitoring and inspections, the Company continues to invest in its safe tailings strategy and is developing a long-term tailings investment plan.
The decrease in stripping and mining activities during the three and six-month periods ended September 30, 2022, compared to the same periods in 2021, is in line with the mine plan, inclusive of Phase II operations. The variation in stripping activities is attributable to the revised stripping ratio used to capitalize some of the mining cost since the fourth quarter of the 2022 financial year. The new ratio considers the Company’s mineral reserves as per the execution of the Phase II mine plan. Higher stripping and mining activities in the comparative periods were associated with the preparation for the Phase II project operations.
The increase in the Company’s mining equipment maintenance program for the three and six-month periods ended September 30, 2022, is attributable to the addition of mining operating equipment and the high utilization rate for this equipment. Mining equipment rebuild expenditures were also negatively affected by global inflation during the three and six-month periods ended September 30, 2022.
Other Capital Development Expenditures at Bloom Lake
During the three-month period ended September 30, 2022, other capital development expenditures at Bloom Lake totalled $42.4 million, compared to $127.2 million in the same period in 2021. During the three-month period ended September 30, 2022, the expenditures mainly consisted of $26.2 million in Phase II capital expenditures, $5.1 million in borrowing costs which were capitalized during the development of the Phase II project, and $4.5 million in deposits for production equipment to be commissioned and financed in the future through the finance agreement with Caterpillar Financial Services Limited. During the three-month period ended September 30, 2022, other capital development expenditures were offset by the receipt of a government grant totalling $5.2 million related to the Company’s greenhouse gas emissions and energy consumption reduction initiatives, compared to $6.2 million in the same prior-year period. The Company qualified for total grants of up to $21.8 million.
During the six-month period ended September 30, 2022, other capital development expenditures at Bloom Lake totalled $138.1 million, compared to $220.4 million in the same prior-year period. During the six-month period ended September 30, 2022, the expenditures mainly consisted of $94.0 million in Phase II capital expenditures, $19.2 million in deposits for production equipment, and $9.6 million in borrowing costs. Other capital development expenditures were offset by the receipt of a government grant totalling $5.2 million as detailed above, compared to $6.2 million in the same period in 2021.
During the three and six-month periods ended September 30, 2021, the expenditures mainly comprised of Phase II capital expenditures, lodging infrastructure investments at the mine site required to accommodate an increasing workforce, prepayments for production equipment and increases in mill capacity and other infrastructure improvements.
About Champion Iron Limited
Champion Iron Limited, through its subsidiary Quebec Iron Ore Inc., owns and operates the Bloom Lake Mining Complex, located on the south end of the Labrador Trough, approximately 13 km north of Fermont, Québec. Bloom Lake is an open-pit operation with two concentrators that primarily source energy from renewable hydroelectric power. The Bloom Lake Phase I and Phase II plants have a combined nameplate capacity of 15 Mtpa and produce a low contaminant high-grade 66.2% Fe iron ore concentrate with a proven ability to produce a 67.5% Fe direct reduction quality concentrate. Bloom Lake’s high-grade and low contaminant iron ore products have attracted a premium to the Platts IODEX 62% Fe iron ore benchmark. The Company ships iron ore concentrate from Bloom Lake by rail, to a ship loading port in Sept-Îles, Québec, and has sold its iron ore concentrate to customers globally, including in China, Japan, the Middle East, Europe, South Korea, India and Canada. In addition to the Bloom Lake Mining Complex, Champion owns a portfolio of exploration and development projects in the Labrador Trough, including the Kamistiatusset Project located a few kilometres south-east of Bloom Lake, and the Consolidated Fire Lake North iron ore project, located approximately 40 km south of Bloom Lake.
Ascot Resources Ltd. (TSX: AOT) (OTCQX: AOTVF) is pleased to anno... READ MORE
Highlights Closing the fully subscribed brokered offering for C$8... READ MORE
Mosaic Minerals Corporation (CSE: MOC) announces that it has sign... READ MORE
First Phosphate Corp. (CSE: PHOS) (OTC: FRSPF) (FSE: KD0) is ple... READ MORE
Prospect Ridge Resources Corp. (CSE: PRR) (OTC: PRRSF) (FRA: OE... READ MORE