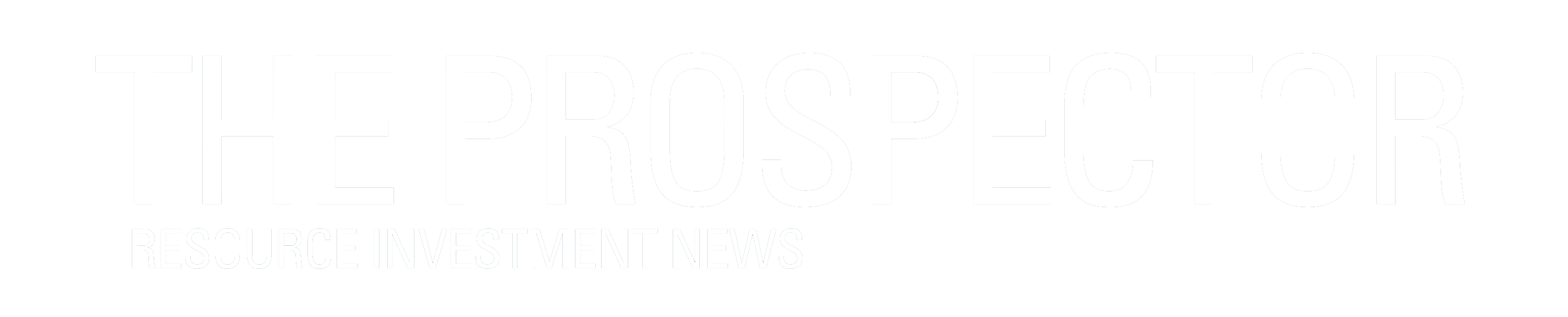
Record quarterly production of 2.3M wmt, Net income of $41.6M, EPS of $0.08 and EBITDA1 of $94.9M;
Bloom Lake Mine Phase II expansion ramping-up as scheduled
Champion Iron Limited (TSX: CIA) (ASX: CIA) (OTCQX: CIAFF) is pleased to announce the operational and financial results for the first quarter ended June 30, 2022, of the financial year ending March 31, 2023.
Champion’s CEO, Mr. David Cataford, said: “Due to the continuous dedication of our workforce and partners, our Company reached another milestone by completing Bloom Lake’s Phase II expansion project and delivering record quarterly production results, even with scheduled semi-annual maintenance. With the progress achieved since commissioning the Phase II expansion, we remain confident in meeting our target to reach commercial production by the end of the calendar year, which should positively impact operational costs per tonne as we ramp up the project. In line with our vision to capitalize on the rising demand for high-purity iron ore products, we continue to evaluate several organic growth projects, which would position our Company as a market leader in the green steel supply chain.”
Health & Safety
Financial
Operations
Growth and Development
Phase II Milestones
Three Months Ended | |||||
June 30, | |||||
2022 | 2021 | Variance | |||
Operating Data | |||||
Waste mined and hauled (wmt) | 5,606,000 | 4,699,500 | 19 % | ||
Ore mined and hauled (wmt) | 6,193,100 | 5,643,900 | 10 % | ||
Material mined and hauled (wmt) | 11,799,100 | 10,343,400 | 14 % | ||
Strip ratio | 0.91 | 0.83 | 10 % | ||
Ore milled (wmt) | 6,022,200 | 5,227,200 | 15 % | ||
Head grade Fe (%) | 31.0 | 29.6 | 5 % | ||
Fe recovery (%) | 80.2 | 82.9 | (3 %) | ||
Product Fe (%) | 66.1 | 66.3 | — % | ||
Iron ore concentrate produced (wmt) | 2,282,600 | 1,936,000 | 18 % | ||
Iron ore concentrate sold (dmt) | 2,013,900 | 1,974,700 | 2 % | ||
Financial Data (in thousands of dollars) | |||||
Revenues | 279,321 | 545,408 | (49 %) | ||
Cost of sales | 169,407 | 120,846 | 40 % | ||
Other expenses | 15,605 | 14,560 | 7 % | ||
Net finance costs | 4,190 | 4,387 | (4 %) | ||
Net income | 41,554 | 224,339 | (81 %) | ||
EBITDA1 | 94,930 | 405,739 | (77 %) | ||
Statistics (in dollars per dmt sold) | |||||
Gross average realized selling price1 | 190.4 | 279.7 | (32 %) | ||
Net average realized selling price1 | 138.7 | 276.2 | (50 %) | ||
Total cash cost (C1 cash cost)1 | 74.0 | 60.1 | 23 % | ||
All-in sustaining cost1 | 93.5 | 72.6 | 29 % | ||
Cash operating margin1 | 45.2 | 203.6 | (78 %) |
Phase II Commissioning
During the three-month period ended June 30, 2022, the Company initiated and advanced the commissioning of Phase II. At the end of April 2022, the Company commissioned the first of two production lines of the Phase II plant and completed its first rail shipments on May 3, 2022. In June 2022, the Company successfully started the second line, reflecting the normal commissioning curve of a new facility. As at June 30, 2022, both lines were in service, positioning the Company to achieve commercial production as scheduled by the end of calendar 20223.
Operational Performance
In the three-month period ended June 30, 2022, 11,799,100 tonnes of material were mined and hauled, compared to 10,343,400 tonnes during the same period in 2021, an increase of 14%. The increase in material movement was enabled through the utilization of additional equipment compared to the same prior-year period, offset by a longer haul cycle as material sourced from different pits, including those that deepened with mining activities over time, contributed to a longer haul cycle year-over-year. The current strip ratio is in line with the mine plan.
The iron ore head grade for the three-month period ended June 30, 2022, was 31.0%, compared to 29.6% for the same period in 2021. The variation in head grade is attributable to the presence of some higher-grade ore being sourced and blended from different pits, which was anticipated and is in line with the mining plan and the LoM head grade average.
The Company’s average Fe recovery rate for the three-month period ended June 30, 2022 was negatively impacted by the anticipated lower recoveries during the commissioning of the Phase II concentrator. The global Fe recovery rate is in line with Management’s expectations at this stage of the Phase II commissioning. The Company expects to reach a stable Fe recovery circuit when Phase II achieves commercial production, anticipated to occur by the end of calendar 2022.
During the three-month periods ended June 30, 2022 and 2021, operational activities were impacted by a scheduled semi-annual maintenance program. During the three-month period ended June 30, 2022, Bloom Lake produced 2,282,600 wmt of 66.1% Fe high-grade iron ore concentrate, an increase of 18%, compared to 1,936,000 wmt of 66.3% Fe during the same period in 2021. The Company achieved record production despite semi-annual scheduled maintenance, in connection with the commissioning of the second plant at the mine site. While the newly commissioned Phase II project’s production compares favourably to the scheduled production volumes, production in the period was negatively impacted by unplanned third-party shutdowns. Higher throughput and head grade also contributed to higher production volumes, despite a lower global recovery. The plants processed 6,022,200 tonnes of ore during the three-month period ended June 30, 2022, compared to 5,227,200 for the same prior-year period. The throughput for the period was positively affected by the higher mined ore availability and the commissioning of Phase II operations.
During the three-month period ended June 30, 2022, 2,013,900 tonnes of high-grade iron ore concentrate were sold at the CFR China gross average realized price1 of US$149.6/dmt, before freight and other costs and provisional pricing adjustments, compared to US$228.3/dmt for the same prior-year period. The decrease in gross average realized selling price1 reflects lower index prices during the three-month period ended June 30, 2022, compared to the same prior-year period. Despite lower index prices, the gross average realized selling price1 of US$149.6/dmt represents a premium of 8.5% over the benchmark IODEX 62% Fe CFR China Index (“P62”) price for the period, compared to a premium of 14.2% for the same period in 2021.
The gross average realized selling price1 of US$149.6/dmt was lower than the IODEX 65% Fe CFR China Index (“P65”) average price of US$160.3/dmt for the period due to the negative impact of sales at a determined price based on the average forward price of US$138.4 at the expected settlement date for 667,600 tonnes which were in transit at the end of the period, and due to the negative impact of sales based on backward-looking iron ore prices, when prices were slightly lower than the P65 index average for the period.
The average C3 Baltic Capesize Index for the three-month period ended June 30, 2022, was US$30.2/t compared to US$26.2/t for the same period in 2021, representing an increase of 15%, which contributed to higher freight costs in the three-month period ended June 30, 2022, compared to the same prior-year period. The elevated freight rates for the period can partially be attributed to the rising fuel prices experienced since the beginning of the conflict in Ukraine. Simultaneously, increased iron ore exports from Brazil and port congestions in China caused by COVID-19 lockdowns further influenced rising freight rates.
Provisional pricing adjustments on previous sales, which were directly correlated to the decrease in the P65 index during the quarter contributed to decreasing the net average realized selling price1. During the three-month period ended June 30, 2022, the final price was established for the 691,100 tonnes of iron ore that were in transit as at March 31, 2022. Accordingly, during the three-month period ended June 30, 2022, net negative provisional pricing adjustments were recorded as a decrease in revenues for the 691,100 tonnes, representing a negative impact of US$6.4/dmt for the period, compared to a positive impact of US$25.3/dmt for the same period in 2021.
After taking into account sea freight and other costs of US$34.4/dmt and the negative provisional pricing adjustment of US$6.4/dmt, the Company obtained a net average realized selling price1 of US$108.8/dmt (CA$138.7/dmt) for its high-grade iron ore delivered to the end customer. Revenues totalled $279,321,000 for the three-month period ended June 30, 2022, compared to $545,408,000 for the same period in 2021, reflecting the lower net average realized selling price1 partially offset by the positive impact of foreign exchange rates and slightly higher sales volume.
Cost of sales represents mining, processing, and mine site-related G&A expenses as well as rail and port operation costs. It also includes specific and incremental costs related to COVID-19 and, starting in April 2022, it includes Bloom Lake Phase II start-up costs incurred after the commissioning. These start-up costs include mainly abnormal operational costs attributable to the facility not having reached the normalized level of output. For the three-month period ended June 30, 2022, the cost of sales totalled $169,407,000, compared to $120,846,000 for the same period in 2021.
During the three-month period ended June 30, 2022, the total cash cost1 or C1 cash cost1 per tonne, excluding specific and incremental costs related to COVID-19 and Phase II start-up costs, totalled $74.0/dmt, compared to $60.1/dmt for the same period in 2021. The total cash cost1 for the three-month period ended June 30, 2022, was negatively impacted by global market inflation. The higher cash cost1 for the period was attributable to record prices for fuel and explosives, and cost increases in key supplies and other consumables, air transportation, food, as well as rail and port operations. Higher labour costs and longer haul cycle times associated with the current mine plan also contributed to a higher cash cost1 during the period. Unplanned third-party shutdowns, planned maintenance of additional facilities and increased headcount and subcontractor usage in relation to the commissioning of the Phase II project also contributed to a higher cost of sales for the period.
For the three-month period ended June 30, 2022, the Company generated net income of $41,554,000 (EPS of $0.08), compared to $224,339,000 (EPS of $0.44) for the same period in 2021. The net income was mainly affected by lower gross profits associated with a lower P65 index average price, higher sea freight and other costs during the period, as well as higher cash cost1, compared to the same prior-year period. The decrease in net income is partially offset by lower current income and mining taxes as a result of lower operating earnings.
For the three-month period ended June 30, 2022, the Company generated EBITDA1 of $94,930,000, representing an EBITDA margin1 of 34%, compared to $405,739,000, representing an EBITDA margin1 of 74% for the same period in 2021. The decrease in EBITDA1 period-over-period is primarily due to lower revenue from lower net average realized selling prices1 and higher cash cost1.
During the three-month period ended June 30, 2022, the Company realized an AISC1 of $93.5/dmt, compared to $72.6/dmt for the same period in 2021. The variation relates to higher total cash costs1, sustaining capital expenditures and additional G&A expenses, partially offset by the slightly positive impact of higher volumes of iron ore concentrate sold. The Company is actively working to ensure everything is in place to support Phase II operations, including hiring additional personnel and incurring the necessary sustaining capital expenditures. This negatively impacted costs during the three-month period ended June 30, 2022, as sales related to Phase II operations gradually increased, while upfront preparation-related costs aim to support Bloom Lake’s revised nameplate capacity.
Deducting the AISC1 of $93.5/dmt from the net average realized selling price1 of $138.7/dmt, the Company generated a cash operating margin1 of $45.2/dmt for each tonne of high-grade iron ore concentrate sold during the three-month period ended June 30, 2022, compared to $203.6/dmt for the same prior-year period. The variation is mainly due to a lower net average realized selling price1 for the period.
During the three-month period ended June 30, 2022, the Company maintained all of its properties in good standing and did not enter into any farm-in/farm-out arrangements. During the three-month period ended June 30, 2022, $2,132,000 in exploration and evaluation expenditures were incurred, compared to $743,000 for the same period in 2021. During the three-month period ended June 30, 2022, exploration and evaluation expenditures mainly consisted of costs associated with resource development and drilling, work related to updating the Kami Project feasibility study and claim renewal fees. During the three-month period ended June 30, 2022, 3,637 metres of diamond drilling was completed on the Bloom Lake property. Drilling at Bloom Lake was undertaken mainly for the conversion of resources. In the comparative period, exploration and evaluation expenditures mainly consisted of costs associated with minor exploration work and preliminary work related to updating the Kami Project feasibility study.
Details on exploration projects and maps are available on the Company’s website at www.championiron.com under the section Operations & Projects.
During the three-month period ended June 30, 2022, the Company invested $122,614,000 in property, plant and equipment, compared to $109,939,000 for the same period in 2021. The following table details these investments:
Three Months Ended | ||||
June 30, | ||||
2022 | 2021 | |||
(in thousands of dollars) | ||||
Tailings lifts | 8,985 | 6,338 | ||
Stripping and mining activities | 11,063 | 8,534 | ||
Mining equipment rebuild | 6,897 | 1,895 | ||
Sustaining capital expenditures | 26,945 | 16,767 | ||
Other capital development expenditures at Bloom Lake | 95,669 | 93,172 | ||
Purchase of property, plant and equipment as per cash flows | 122,614 | 109,939 |
Sustaining Capital Expenditures
The increase in tailings-related investments for the three-month period ended June 30, 2022, compared to the same period in 2021, is mainly due to the timing of expenditures incurred on the dikes. During the three-month period ended June 30, 2022, weather conditions were more favourable than the same prior-year period, enabling the Company to advance work performed on the dikes. As part of the Company’s ongoing and thorough tailings infrastructure monitoring and inspections, the Company continues to invest in its safe tailings strategy.
The increase in stripping and mining activities during the three-month period ended June 30, 2022, compared to the same period in 2021, is in line with the mine plan, inclusive of Phase II operations. The variation in stripping activities is also attributable to the revised stripping ratio used for cost capitalization since the fourth quarter of the 2022 financial year, following changes in the Company’s mineral reserves as per the execution of the Phase II mine plan.
The increase in the Company’s mining equipment maintenance program for the three-month period ended June 30, 2022, is attributable to the additional mining operating equipment and a high utilization rate of this equipment. Mining equipment rebuild expenditures were also negatively affected by global inflation during the three-month period ended June 30, 2022.
Other Capital Development Expenditures at Bloom Lake
During the three-month period ended June 30, 2022, other capital development expenditures at Bloom Lake totalled $95,669,000. The expenditures mainly consisted of $67,842,000 in Phase II capital expenditures, $14,781,000 in deposits for production equipment to be commissioned and financed in the future through the finance agreement with Caterpillar Financial Services Limited, and $4,421,000 in borrowing costs which were capitalized during the development of the Phase II project.
During the three-month period ended June 30, 2021, other capital development expenditures at Bloom Lake totalled $93,172,000 and were mainly comprised of $77,925,000 spent in Phase II capital expenditures. The investment for the three-month period ended June 30, 2021, also consisted of lodging infrastructure investments at the mine site required to accommodate an increasing workforce, prepayments for production equipment and increases in mill capacity and other infrastructure improvements.
About Champion Iron Limited
Champion Iron Limited, through its subsidiary Quebec Iron Ore Inc., owns and operates the Bloom Lake Mining Complex, located on the south end of the Labrador Trough, approximately 13 km north of Fermont, Québec. Bloom Lake is an open-pit operation with two concentrators that primarily source energy from renewable hydroelectric power. The Bloom Lake Phase I and Phase II plants have a combined nameplate capacity of 15 Mtpa and produce a low contaminant high-grade 66.2% Fe iron ore concentrate with a proven ability to produce a 67.5% Fe direct reduction quality concentrate. Bloom Lake’s high-grade and low contaminant iron ore products have attracted a premium to the Platts IODEX 62% Fe iron ore benchmark. The Company ships iron ore concentrate from Bloom Lake by rail, to a ship loading port in Sept-Îles, Québec, and sells its iron ore concentrate to customers globally, including in China, Japan, the Middle East, Europe, South Korea, India and Canada. In addition to the Bloom Lake Mining Complex, Champion owns a portfolio of exploration and development projects in the Labrador Trough, including the Kamistiatusset Project located a few kilometres south-east of Bloom Lake, and the Consolidated Fire Lake North iron ore project, located approximately 40 km south of Bloom Lake.
Non-IFRS and Other Financial Measures
The Company has included certain non-IFRS financial measures, ratios and supplementary financial measures in this press release, as listed in the table below, to provide investors with additional information in order to help them evaluate the underlying performance of the Company. These measures are mainly derived from the Financial Statements but do not have any standardized meaning prescribed by IFRS and, therefore, may not be comparable to similar measures presented by other companies. Management believes that these measures, in addition to conventional measures prepared in accordance with IFRS, provide investors with an improved ability to understand the results of the Company’s operations. Non-IFRS and other financial measures should not be considered in isolation or as a substitute for measures of performance prepared in accordance with IFRS. The exclusion of certain items from non-IFRS financial measures does not imply that these items are necessarily non-recurring.
Non-IFRS and Other Financial Measures | |
Non-IFRS Financial Measures | |
EBITDA | Earnings before income and mining taxes, net finance costs and depreciation |
Adjusted net income | Net income plus incremental costs related to COVID-19 and Bloom Lake Phase II start-up costs, less gain on disposal of non-current investments, and the related tax effect of these items |
Available liquidity | Cash and cash equivalents plus short-term investments plus undrawn amounts under credit facilities |
Non-IFRS Ratios | |
EBITDA margin | EBITDA as a percentage of revenues |
Adjusted EPS | Adjusted net income per basic weighted average number of ordinary shares outstanding |
Total cash cost or C1 cash cost per dmt sold | Cost of sales before incremental costs related to COVID-19 and Bloom Lake Phase II start-up costs divided by iron ore concentrate sold in dmt |
AISC per dmt sold | Cost of sales before incremental costs related to COVID-19 and Bloom Lake Phase II start-up costs plus sustaining capital expenditures and G&A expenses divided by iron ore concentrate sold in dmt |
Cash operating margin | Net average realized selling price less AISC |
Gross average realized selling price or gross average realized FOB selling price per dmt sold | Revenues before provisional pricing adjustments and freight and other costs divided by iron ore concentrate sold in dmt |
Cash profit margin | Cash operating margin as a percentage of net average realized selling price |
Other Financial Measures | |
Net average realized selling price or net average realized FOB selling price per dmt sold | Revenues divided by iron ore concentrate sold in dmt |
Operating cash flow per share | Net cash flow from (used in) operating activities per basic weighted average number of ordinary shares outstanding |
EBITDA and EBITDA Margin
Three Months Ended | ||||
June 30, | ||||
2022 | 2021 | |||
(in thousands of dollars) | ||||
Income before income and mining taxes | 70,948 | 391,393 | ||
Net finance costs | 4,190 | 4,387 | ||
Depreciation | 19,792 | 9,959 | ||
EBITDA | 94,930 | 405,739 | ||
Revenues | 279,321 | 545,408 | ||
EBITDA margin | 34 % | 74 % |
Adjusted Net Income and Adjusted EPS
Three Months Ended | ||||
June 30, 2022 | ||||
Net Income | EPS | |||
Unadjusted | 41,554 | 0.08 | ||
Cash items | ||||
Gain on disposal of non-current investments | — | — | ||
Incremental costs related to COVID-19 | 840 | — | ||
Bloom Lake Phase II start-up costs | 19,476 | 0.04 | ||
20,316 | 0.04 | |||
Tax effect of adjustments listed above1 | (7,720) | (0.02) | ||
Adjusted | 54,150 | 0.10 |
Three Months Ended | ||||
June 30, 2021 | ||||
Net Income | EPS | |||
Unadjusted | 224,339 | 0.44 | ||
Cash items | ||||
Gain on disposal of non-current investments | (408) | — | ||
Incremental costs related to COVID-19 | 2,068 | — | ||
1,660 | — | |||
Tax effect of adjustments listed above1 | (889) | — | ||
Adjusted | 225,110 | 0.44 | ||
1 The tax effect of adjustments is calculated using the applicable tax rate. |
Available Liquidity
As at June 30, | As at March 31, | |||
2022 | 2022 | |||
Cash and cash equivalents | 155,924 | 321,892 | ||
Short-term investments | 31,161 | 30,777 | ||
Undrawn amounts under credit facilities | 383,941 | 393,303 | ||
Available liquidity | 571,026 | 745,972 |
Total Cash Cost
Three Months Ended | ||||
June 30, | ||||
2022 | 2021 | |||
Per tonne sold | ||||
Iron ore concentrate sold (dmt) | 2,013,900 | 1,974,700 | ||
(in thousands of dollars except per tonne) | ||||
Cost of sales | 169,407 | 120,846 | ||
Less: Incremental costs related to COVID-19 | (840) | (2,068) | ||
Less: Bloom Lake Phase II start-up costs | (19,476) | — | ||
149,091 | 118,778 | |||
Total cash cost (per dmt sold) | 74.0 | 60.1 |
All-In Sustaining Cost
Three Months Ended | ||||
June 30, | ||||
2022 | 2021 | |||
Per tonne sold | ||||
Iron ore concentrate sold (dmt) | 2,013,900 | 1,974,700 | ||
(in thousands of dollars except per tonne) | ||||
Cost of sales | 169,407 | 120,846 | ||
Less: Incremental costs related to COVID-19 | (840) | (2,068) | ||
Less: Bloom Lake Phase II start-up costs | (19,476) | — | ||
Sustaining capital expenditures | 26,945 | 16,767 | ||
G&A expenses | 12,272 | 7,804 | ||
188,308 | 143,349 | |||
AISC (per dmt sold) | 93.5 | 72.6 |
Cash Operating Margin and Cash Profit Margin
Three Months Ended | ||||
June 30, | ||||
2022 | 2021 | |||
Per tonne sold | ||||
Iron ore concentrate sold (dmt) | 2,013,900 | 1,974,700 | ||
(in thousands of dollars except per tonne) | ||||
Revenues | 279,321 | 545,408 | ||
Net average realized selling price (per dmt sold) | 138.7 | 276.2 | ||
AISC (per dmt sold) | 93.5 | 72.6 | ||
Cash operating margin (per dmt sold) | 45.2 | 203.6 | ||
Cash profit margin | 33 % | 74 % |
Gross Average Realized Selling Price per dmt Sold
Three Months Ended | |||
June 30, | |||
2022 | 2021 | ||
Per tonne sold | |||
Iron ore concentrate sold (dmt) | 2,013,900 | 1,974,700 | |
(in thousands of dollars except per tonne) | |||
Revenues | 279,321 | 545,408 | |
Provisional pricing adjustments | 15,668 | (60,895) | |
Freight and other costs | 88,757 | 67,807 | |
Gross revenues | 383,746 | 552,320 | |
Gross average realized selling price (per dmt sold) | 190.5 | 279.7 |
Lode Gold Resources Inc. (TSX-V: LOD) (OTCQB: LODFF) is pleased t... READ MORE
Pacific Ridge Exploration Ltd. (TSX-V: PEX) (OTCQB: PEXZF) (FSE: ... READ MORE
Purepoint Uranium Group Inc. (TSX-V: PTU) (OTCQB: PTUUF) announce... READ MORE
New Found Gold Corp. (TSX-V: NFG) (NYSE American: NFGC) and Marit... READ MORE
Elemental Altus Royalties Corp. (TSX-V: ELE) (OTCQX: ELEMF) and E... READ MORE