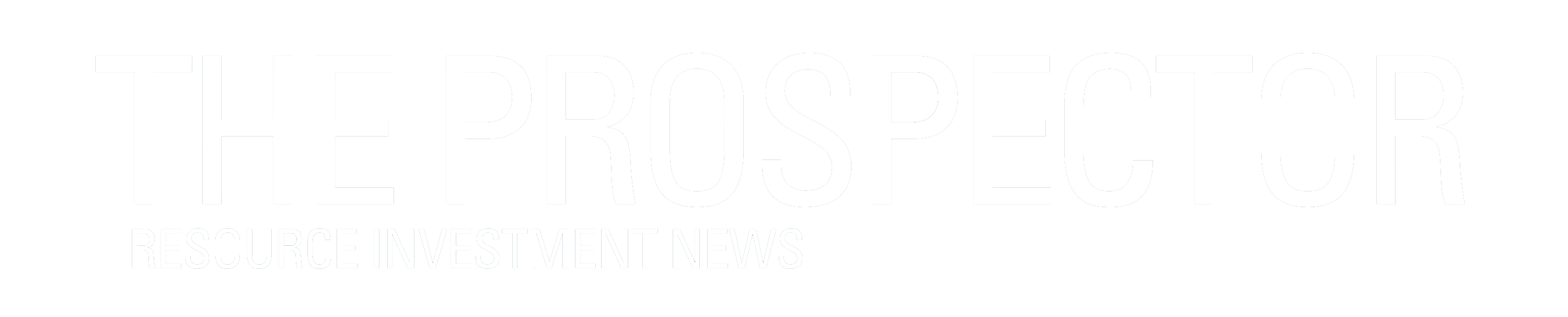
Champion Iron Limited (TSX: CIA) (ASX: CIA) (OTCQX: CIAFF) is pleased to announce its operational and financial results for the 2024 financial year second quarter ended September 30, 2023.
Champion’s CEO, Mr. David Cataford, said: “Thanks to its agility, our team achieved a new quarterly production record of 3.45 million wmt. Following the quarter end, our team realized the full potential of Bloom Lake with production levels now reaching its expanded nameplate capacity of 15 Mtpa in the most recent 30 days. Our operating costs per tonne are also on track to continue improving as we benefit from continuous optimization work programs. Additionally, we remain confident in our ability to advance the Direct Reduction Pellet Feed Project (“DRPF Project”) to potential completion by the second half of calendar 2025. This project will not only continue to benefit the Québec Côte-Nord region, but it is also essential for supplying a critical raw material required for the accelerating shift towards green steelmaking.”
Sustainability and Health & Safety
Operations and Finance
Direct Reduction Pellet Feed Project Update
Other Growth and Development
Three Months Ended | Six Months Ended | |||||||
September 30, | September 30, | |||||||
2023 | 2022 | Variance | 2023 | 2022 | Variance | |||
Operating Data | ||||||||
Waste mined and hauled (wmt) | 6,264,600 | 4,572,900 | 37 % | 11,463,100 | 10,178,900 | 13 % | ||
Ore mined and hauled (wmt) | 10,593,600 | 8,214,700 | 29 % | 20,187,100 | 14,407,800 | 40 % | ||
Material mined and hauled (wmt) | 16,858,200 | 12,787,600 | 32 % | 31,650,200 | 24,586,700 | 29 % | ||
Stripping ratio | 0.59 | 0.56 | 5 % | 0.57 | 0.71 | (20 %) | ||
Ore milled (wmt) | 10,339,700 | 8,102,700 | 28 % | 20,235,300 | 14,124,900 | 43 % | ||
Head grade Fe (%) | 28.2 | 29.5 | (4 %) | 28.5 | 30.2 | (6 %) | ||
Fe recovery (%) | 77.8 | 78.6 | (1 %) | 78.0 | 79.3 | (2 %) | ||
Product Fe (%) | 66.1 | 66.1 | — % | 66.1 | 66.1 | — % | ||
Iron ore concentrate produced (wmt) | 3,447,200 | 2,857,300 | 21 % | 6,844,400 | 5,139,900 | 33 % | ||
Iron ore concentrate sold (dmt) | 2,883,800 | 2,793,400 | 3 % | 5,447,300 | 4,807,300 | 13 % |
Impact of Forest Fires
Forest fires emerged on May 28, 2023, north of Sept-Îles, Québec, resulting in railway service interruptions between Bloom Lake and the port of Sept-Îles between May 30 and June 10, 2023. There was no damage to Champion’s facilities and no significant damage was identified to the railway following inspections by its operator besides the destruction of the power and communication line on the affected rail sections. As forest fires subsided in the region, railway services resumed at partial capacity on June 10, 2023, until they returned to normal levels during the quarter ended September 30, 2023, after repairs to the damaged electrical poles and wires over several kilometers were completed. As a result, shipments and sales were impacted in the first half of the 2024 financial year.
Despite supply chain challenges caused by multiple highway closures impacting operations, Bloom Lake operated continuously throughout the railway interruptions and stockpiled iron ore concentrate at the mining complex. The Company responded to the situation by triggering its emergency response plan and managed supply chain risks by focusing mine operations on critical activities required to feed the two plants. This impacted the Company’s ability to move waste and generate blasted ore inventory in the first quarter of the 2024 financial year. The Company also used its crusher’s stockpiles to supply the two plants during that period and suffered from a short power outage which impacted operations for a full day.
As at September 30, 2023, the Company had 1.6 million wmt of iron ore concentrate in inventory at the Bloom Lake site. Although the recent commissioning of three additional locomotives received in June 2023 had a positive impact on the volume of concentrate transported to Sept-Îles, it was offset by an annual planned maintenance shutdown of the railway facilities lasting several days and its reduced capacity in the first half of the quarter, as well as a few days’ outage caused by a train derailment. The Company and its rail service provider are working diligently to maximize the transportation of tonnes from Bloom Lake to Sept-Îles. The Company expects its stockpiled iron ore concentrate at Bloom Lake to be shipped and sold over several upcoming quarters. The Company also expects to incur additional rehandling costs in future periods to reclaim the iron ore concentrate from the stockpile.
Phase II Update
Phase II reached commercial production in December 2022 and the Company continued to make improvements to stabilize and optimize operations. As expected when delivering a project of this scale, the Company faced challenges, including delays in deliveries and commissioning of mining equipment, creating inefficiencies across the site, which negatively impacted the Company’s ability to reach its full expanded nameplate capacity. Phase II produced at nameplate capacity for thirty consecutive days for the first time during the first quarter of the 2024 financial year. Considering its success in increasing its production at the mine and ore material milled quarter after quarter, and ongoing work programs, the Company continues its progress towards reaching its expanded 15 Mtpa production nameplate capacity on a consistent basis. Those programs aim to increase throughput and ore recoveries, optimize and synchronize operations, and adapt maintenance practices.
The main Phase II work on third-party infrastructure was completed in the three-month period ended September 30, 2023, further positioning the Company to benefit from additional flexibility and capacity to handle the Company’s expanded nameplate capacity at the port facilities in Sept-Îles. The recent commissioning of the stacker reclaimer and associated conveyors, and three additional locomotives required to support the expanded production capacity should positively impact the Company’s shipment capacity and vessel loading time.
Operational Performance
Second Quarter of the 2024 Financial Year vs Second Quarter of the 2023 Financial Year
In the three-month period ended September 30, 2023, 16.9 million tonnes of material were mined and hauled, compared to 12.8 million tonnes during the same period in 2022, an increase of 32%, attributable to the contribution of additional equipment commissioned during the financial year. This also represents a 14% improvement over the volume mined and hauled in the previous quarter due to a higher utilization of mining equipment associated with an increase in the number of operators and better equipment availability. The stripping ratio of 0.59 for the three-month period ended September 30, 2023, is comparable to the same period in 2022, and increased as planned, compared to 0.54 in the previous quarter.
During the three-month period ended September 30, 2023, an unscheduled outage related to a major crusher ore belt failure in one of the Company’s conveyor systems negatively impacted the availability of the Phase II concentrator for several days. Despite this situation, the two plants processed 10.3 million tonnes of ore during the three-month period ended September 30, 2023, compared to 8.1 million tonnes for the same prior-year period, an increase of 28%, driven by the progress of the Phase II ramp-up to reach Bloom Lake’s expanded production nameplate capacity of 15 Mtpa. Material processed by the two plants also increased by 4%, compared to 9.9 million tonnes in the previous quarter, and reached the two mills feed nameplate capacity during the three-month period ended September 30, 2023.
The iron ore head grade for the three-month period ended September 30, 2023, was 28.2%, compared to 29.5% for the same period in 2022, and 28.8% during the previous quarter. The variation in head grade was within expected normal variations in the mine plan.
The Company’s average Fe recovery rate was 77.8% for the three-month period ended September 30, 2023, compared to 78.6% for the same period in 2022, and 78.2% during the previous quarter. In the context of constrained rail capacity, the Company adjusted the mine plan to process more challenging ore from some areas, which negatively impacted recovery rates during the period. The Company remains confident in its ability to reach the average LoM expected Fe recovery rate target of 82.0% in upcoming quarters at Bloom Lake, as detailed in the 2023 Technical Report.
Despite the impact of an unscheduled outage lasting several days to repair a conveyor system, and lower head grade and recovery, the two processing plants delivered a record production of 3.45 million wmt of high-grade iron ore concentrate during the three-month period ended September 30, 2023, an increase of 21% compared to 2.9 million wmt during the same period in 2022 and an increase of 1.5% compared to the previous quarter.
First Six Months of the 2024 Financial Year vs First Six Months of the 2023 Financial Year
The Company mined and hauled 31.7 million tonnes of material during the six-month period ended September 30, 2023, compared to 24.6 million tonnes for the same period in 2022, an increase of 29% driven by additional mining equipment in operation.
The stripping ratio was 0.57 for the six-month period ended September 30, 2023, compared to 0.71 for the same period in 2022, slightly lower than the Company’s plan for the 2024 financial year. The Company strategically focused on mining ore in the first months of the 2024 financial year with a reduced mining equipment capacity and limited fuel reserves caused by supply challenges related to the June 2023 forest fires, as fuel inventories were prioritized for critical activities.
The two plants processed 20.2 million tonnes of ore during the six-month period ended September 30, 2023, an increase of 43% over the same period in 2022, and produced a record of 6.8 million wmt of high-grade iron ore concentrate, compared to 5.1 million wmt for the same period in 2022, benefiting from the Phase II ramp-up.
The iron ore head grade of 28.5% for the six-month period ended September 30, 2023, is consistent with the LoM head grade average. The lower average Fe recovery rate for the six-month period ended September 30, 2023, was mainly attributable to the processing of more challenging ore from some areas in the pits and to a slight backlog in the recovery circuit maintenance due to significant efforts deployed on solving conveying challenges in the past months. Significant improvements were made to increase the reliability and productivity of the Company’s crushed ore conveying systems which should allow the Company to resume its proven ability to stabilize and optimize its recovery circuits.
Three Months Ended | Six Months Ended | |||||||
September 30, | September 30, | |||||||
2023 | 2022 | Variance | 2023 | 2022 | Variance | |||
Financial Data (in thousands of dollars) | ||||||||
Revenues | 387,568 | 300,621 | 29 % | 684,730 | 579,942 | 18 % | ||
Cost of sales | 212,584 | 199,841 | 6 % | 421,069 | 369,248 | 14 % | ||
Other expenses | 20,192 | 16,839 | 20 % | 39,837 | 32,444 | 23 % | ||
Net finance costs | 11,634 | 10,765 | 8 % | 18,560 | 14,955 | 24 % | ||
Net income | 65,281 | 19,530 | 234 % | 81,938 | 61,084 | 34 % | ||
EBITDA1 | 155,036 | 84,331 | 84 % | 220,841 | 179,261 | 23 % | ||
Statistics (in dollars per dmt sold) | ||||||||
Gross average realized selling price1 | 169.4 | 157.0 | 8 % | 169.1 | 171.0 | (1 %) | ||
Net average realized selling price1 | 134.4 | 107.6 | 25 % | 125.7 | 120.6 | 4 % | ||
C1 cash cost1 | 73.7 | 65.9 | 12 % | 77.3 | 69.3 | 12 % | ||
AISC1 | 99.1 | 81.9 | 21 % | 96.7 | 86.8 | 11 % | ||
Cash operating margin1 | 35.3 | 25.7 | 37 % | 29.0 | 33.8 | (14 %) |
Second Quarter of the 2024 Financial Year vs Second Quarter of the 2023 Financial Year
Revenues totalled $387.6 million for the three-month period ended September 30, 2023, compared to $300.6 million for the same period in 2022, due to a higher IODEX 65% Fe CFR China Index (“P65”), lower freight and other costs, a weaker Canadian dollar over the same prior-year period and a slight increase in sales volume to 2.9 million tonnes of high-grade iron ore concentrate, compared to 2.8 million tonnes for the same period in 2022.
As expected, sales volume for the period was affected by the reduced railway capacity at the beginning of the quarter due to the forest fires in June 2023 and a scheduled maintenance of the railway facilities lasting several days. A few days’ unplanned interruption caused by a train derailment, which fortunately caused no injuries or environmental impact, also restricted the transport of iron ore concentrate to the port of Sept-Îles. With additional locomotives in service and rail operations resuming at full capacity, the Company expects its tonnage sold to exceed tonnage produced as it clears iron ore concentrate inventories at the mine site in upcoming periods.
The gross average realized price was US$126.2/dmt1 during the second quarter of the 2024 financial year, up from US$120.6/dmt1 for the same period last year, due to higher P65 index prices. During the three-month period ended September 30, 2023, the P65 index averaged US$125.0/dmt, an increase of 8% from the same quarter last year, representing a premium of 9.6% over the IODEX 62% Fe CFR China Index (“P62”) average price of US$114.0/dmt. Last year, the high-grade premium over the P62 index averaged 11.8%. The decline in premiums for high-grade iron ore for the quarter was mainly due to lower European steel output, a key consuming region for high-grade iron ore, struggling profitability at global steel mills together with the robust seasonal seaborn supply of high-grade iron ore.
The gross average realized selling price of US$126.2/dmt1 was higher than the P65 index average price of US$125.0/dmt for the period, due to the 1.3 million tonnes in transit as at September 30, 2023, that were provisionally priced using an average forward price of US$125.9/dmt, which is higher than the P65 index average price for the period. Gross selling price on sale contracts using backward-looking iron ore index prices for the three-month period ended September 30, 2023, were also slightly higher than to the P65 index average price for the period.
The average C3 Baltic Capesize Index for the three-month period ended September 30, 2023, was US$20.3/t compared to US$24.0/t for the same period in 2022, representing a decrease of 15%, comparable to the decrease in the Company’s freight and other costs in the three-month period ended September 30, 2023. While the C3 index declined from the previous quarter average of US$21.1/t, the Company’s freight cost increased quarter on quarter to US$26.4/dmt due to sales contracts using backward-looking C3 index prices.
Provisional pricing adjustments on previous quarterly sales of $1.6 million were recorded during the three-month period ended September 30, 2023, representing a positive impact of US$0.5/dmt over the total volume of 2.9 million dmt sold during the period. This was due to a slight increase in the P65 index in the first half of the quarter. During the three-month period ended September 30, 2023, a final average price of US$122.4/dmt was established for the 1.4 million tonnes of iron ore that were in transit as at June 30, 2023, and which were previously evaluated using an average expected price of US$121.2/dmt.
After taking into account sea freight and other costs of US$26.4/dmt and the positive provisional pricing adjustment of US$0.5/dmt, the Company obtained a net average realized selling price of US$100.3/dmt (C$134.4/dmt)1 for its high-grade iron ore shipped during the period.
First Six Months of the 2024 Financial Year vs First Six Months of the 2023 Financial Year
Revenues totalled $684.7 million for the six-month period ended September 30, 2023, compared to $579.9 million for the same period in 2022, due to higher sales and higher net average realized selling prices in Canadian dollars, attributable to the weaker Canadian dollar over the same prior-year period.
For the six-month period ended September 30, 2023, the Company sold 5.4 million tonnes of iron ore concentrate, compared to 4.8 million tonnes for the same prior-year period. This represents an increase of 13% year-over-year due to Phase II achieving commercial production in December 2022. Sales volumes during the six-month period ended September 30, 2023, were negatively impacted by twelve days of railway interruptions from May 30 to June 10, 2023, due to forest fires in Québec and reduced service capacity extending into the early part of the second quarter ended September 30, 2023. As discussed above, shipments during the first half of the financial year were also impacted by planned and unplanned rail service interruptions.
The high-grade iron ore P65 index price averaged US$124.5/dmt for the six-month period ended September 30, 2023, representing a decrease of 9% from the period last year. The Company sold its product at a gross average realized selling price of US$126.0/dmt1. Benefiting from a premium product, the Company expects its iron ore concentrate pricing to continue tracking the P65 index in the long term. Deducting sea freight and other costs of US$26.1/dmt and the negative provisional pricing adjustments of US$6.1/dmt, the Company obtained a net average realized selling price of US$93.8/dmt (C$125.7/dmt)1 for its high-grade iron ore concentrate.
Second Quarter of the 2024 Financial Year vs Second Quarter of the 2023 Financial Year
For the three-month period ended September 30, 2023, the cost of sales totalled $212.6 million with a cost of sales per tonne sold of $73.7/dmt1, compared to $199.8 million and $71.5/dmt1 for the same period in 2022. The cost of sales per dmt sold dropped significantly during the three-month period ended September 30, 2023, as expected, compared to $81.3/dmt1 for the first quarter, with increased shipments and semi-annual fuel price adjustments based on trailing prices, positively impacting rail service costs.
The cost of sales for the three-month period ended September 30, 2023, continued to be negatively impacted by the utilization of contractors to fill vacant positions, high maintenance costs relating to planned and unplanned maintenance activities, including costs associated with a breakdown in one of the Company’s conveyor systems and below normal run rate shipment levels during the quarter to amortize mostly fixed costs at the port facilities in Sept-Îles. The Company also incurred rehandling costs at the mine site during the period. This was partially mitigated by lower fuel and explosives prices, and higher production levels.
Mining and processing costs for the 3.4 million dmt produced in the three-month period ended September 30, 2023, totalled $47.3/dmt produced, a decrease of 6% compared to $50.3/dmt produced in the first quarter of the 2024 financial year, reflecting a stronger mining performance.
First Six Months of the 2024 Financial Year vs First Six Months of the 2023 Financial Year
For the six-month period ended September 30, 2023, the cost of sales totalled $421.1 million, compared to $369.2 million for the same period in 2022, with cost of sales per tonne sold of $77.3/dmt1, compared to $76.8/dmt1 for the six-month period ended September 30, 2022.
The cost of sales for the six-month period ended September 30, 2023, was impacted by the same factors that affected the cost of sales for the second quarter ended September 30, 2023.
Mining and processing costs for the 6.6 million dmt produced in the six-month period ended September 30, 2023, totalled $48.8/dmt produced, compared to $45.6/dmt produced in the same prior-year period.
Due to the high stockpile levels at the mine site, attributable to railway interruptions, the Company expects to incur additional rehandling costs to reclaim the iron ore concentrate from the stockpile to rail it to the port, which should negatively impact the cost of sales in future periods.
Second Quarter of the 2024 Financial Year vs Second Quarter of the 2023 Financial Year
For the three-month period ended September 30, 2023, the Company generated EBITDA of $155.0 million1, representing an EBITDA margin of 40%1, compared to $84.3 million1, representing an EBITDA margin of 28%1, for the same period in 2022. Higher EBITDA was mainly due to higher revenues, as described above.
For the three-month period ended September 30, 2023, the Company generated net income of $65.3 million (EPS of $0.13), compared to $19.5 million (EPS of $0.04) for the same period last year. The year-over-year increase in net income is attributable to higher gross profits partially offset by higher current income and mining taxes.
First Six Months of the 2024 Financial Year vs First Six Months of the 2023 Financial Year
For the six-month period ended September 30, 2023, the Company generated EBITDA of $220.8 million1, representing an EBITDA margin of 32%1, compared to $179.3 million1, representing an EBITDA margin of 31%1, for the same prior-year period. This year-over-year increase in EBITDA is mainly attributable to higher sales volumes following the commissioning of Phase II and the increase in the net average realized selling price in Canadian dollars due to the weaker Canadian dollar over the same prior-year period, partially offset by higher production costs.
For the six-month period ended September 30, 2023, the Company generated net income of $81.9 million (EPS of $0.16), compared to $61.1 million (EPS of $0.12) for the same prior-year period. The year-over-year increase in net income is mainly due to higher gross profit.
During the three-month period ended September 30, 2023, the Company realized an AISC of $99.1/dmt1, compared to $81.9/dmt1 for the same period in 2022. The increase was due to higher C1 cash costs, higher sustaining capital expenditures and G&A expenses. Refer to section 5 — Cash Flows – Purchase of Property, Plant and Equipment for details on sustaining capital expenditures.
The Company generated a cash operating margin of $35.3/dmt1 for each tonne of high-grade iron ore concentrate sold during the three-month period ended September 30, 2023, compared to $25.7/dmt1 for the same prior-year period. The variation is mainly due to a higher net average realized selling price for the period, partially offset by higher AISC.
During the six-month period ended September 30, 2023, the Company recorded an AISC of $96.7/dmt1, compared to $86.8/dmt1 for the same period in 2022. The increase was due to higher C1 cash costs as well as higher sustaining capital expenditures and G&A expenses per dmt sold.
The cash operating margin totalled $29.0/dmt1 for the six-month period ended September 30, 2023, compared to $33.8/dmt1 for the same prior-year period. The variation is mainly due to higher AISC, partially offset by a higher net average realized selling price in Canadian dollars.
Bloom Lake Mineral Resources and Reserves Update
The 2023 Technical Report, which was filed on October 3, 2023, confirmed the 18 years’ LoM based on the mineral reserves with an average LoM yearly production of 15.2 million wmt of high purity iron ore concentrate at 66.2% Fe, an average iron metallurgical recovery of 82.0% and plant feed grade of 28.6% Fe. The 2023 Technical Report also confirmed an expansion opportunity considering a 40% increase to the measured and indicated resources and a 360% increase to the inferred resources.
The Company is not aware of any new information or data that materially affects the information included in the 2023 Technical Report and confirms that all material assumptions and technical parameters underpinning the estimates in the 2023 Technical Report continue to apply and have not materially changed.
The 2023 Technical Report can be found under the Company’s profile on SEDAR+ at www.sedarplus.ca.
Exploration and Evaluation Activities
During the three and six-month periods ended September 30, 2023, the Company maintained all of its properties in good standing and did not enter into any farm-in/farm-out arrangements. During the three and six-month periods ended September 30, 2023, $4.6 million and $7.3 million in exploration and evaluation expenditures were incurred, respectively, compared to $0.9 million and $3.1 million, respectively, for the same prior-year periods. During the three and six-month periods ended September 30, 2023, exploration and evaluation expenditures mainly consisted of costs associated with work related to updating the Kami Project feasibility study, claim renewal fees and claim staking around the Kami property. In addition, the Company started a 2000 metres diamond drill campaign for hydro geological characterization in September 2023, expected to be completed by the end of 2023. Details on exploration projects and maps are available on the Company’s website at www.championiron.com under the section Operations & Projects.
Three Months Ended | Six Months Ended | |||||||
September 30, | September 30, | |||||||
2023 | 2022 | 2023 | 2022 | |||||
(in thousands of dollars) | ||||||||
Tailings lifts | 43,041 | 28,440 | 54,987 | 37,425 | ||||
Stripping and mining activities | 6,542 | 3,730 | 9,805 | 14,793 | ||||
Mining equipment rebuild and replacement | 10,683 | 4,011 | 15,235 | 10,908 | ||||
Other sustaining capital expenditures | 180 | — | 222 | — | ||||
Sustaining capital expenditures | 60,446 | 36,181 | 80,249 | 63,126 | ||||
DRPF Project | 16,938 | — | 28,021 | — | ||||
Other capital development expenditures at Bloom Lake | 13,002 | 42,403 | 37,786 | 138,072 | ||||
Purchase of property, plant and equipment as per cash flows | 90,386 | 78,584 | 146,056 | 201,198 |
Sustaining Capital Expenditures
The increases in tailings-related investments for the three and six-month periods ended September 30, 2023, are part of the Company’s long-term plan to prepare the site for a higher level of operations with the commissioning of Phase II. As part of the Company’s ongoing and thorough tailings infrastructure monitoring and inspections, the Company continues to invest in its safe tailings strategy and is implementing its long-term tailings investment plan.
The increase in stripping and mining activities during the three-month period ended September 30, 2023, compared to the same period in the previous financial year, is mainly attributable to investments made for the ongoing construction of additional access ramps for $1.8 million. No stripping cost was capitalized during the three-month period ended September 30, 2023. The decrease in stripping and mining activities during the six-month period ended September 30, 2023, is due to the low level of waste moved at the mine due to limited mining equipment availability early in the period, until all equipment was fully commissioned. The stripping and mining activities for the six-month period ended September 30, 2023, were slightly lower than the Company’s plan for the 2024 financial year, due to the prioritization of critical activities to mitigate the impacts of the forest fires in the first quarter.
The increase in the Company’s mining equipment rebuild program for the three and six-month periods ended September 30, 2023, is attributable to the major overhaul of its growing mining fleet over the last two years to prepare for additional mining activities driven by the Company’s expansion. The mining equipment rebuild program is in line with the Company’s fleet management program for the 2024 financial year.
DRPF Project
During the three and six-month periods ended September 30, 2023, $16.9 million and $28.0 million, respectively, were spent in capital expenditures related to the DRPF Project. Investments mainly consisted of on-site preparation activities, engineering work and long lead-time equipment purchasing. Cumulative investments of $28.9 million were deployed on the DRPF Project as at September 30, 2023.
Other Capital Development Expenditures at Bloom Lake
During the three-month period ended September 30, 2023, other capital development expenditures at Bloom Lake totalled $13.0 million, compared to $42.4 million in the same 2022 period. During the three-month period ended September 30, 2023, the expenditures mainly consisted of $5.6 million in infrastructure improvements and conformity ($7.1 million for the same period last year), $6.8 million for the garage expansion to support the expanded fleet, and $5.1 million in deposits for mining equipment ($4.5 million for the same period last year). The expenditures for the same period last year also included $26.2 million related to Phase II and $5.1 million in capitalized borrowing costs. During the three-month periods ended September 30, 2023 and 2022, other capital development expenditures were partially offset by the receipt of a government grant of $5.2M related to the Company’s greenhouse gas emissions and energy consumption reduction initiatives.
During the six-month period ended September 30, 2023, other capital development expenditures at Bloom Lake totalled $37.8 million, compared to $138.1 million in the same prior-year period. During the six-month period ended September 30, 2023, the expenditures mainly consisted of $14.6 million in infrastructure improvements and conformity ($9.9 million for the same period last year), including the construction of two pads to expand the mine’s capacity to stockpile concentrate near the loadout, $15.2 million for the expansion of the garage, and $11.7 million in deposits for mining equipment ($19.2 million for the same period last year). The expenditures for the first six-month period of last year also included $94.0 million related to Phase II and $9.6 million in capitalized borrowing costs.
Mr. Vincent Blanchet, P. Eng., Engineer at Quebec Iron Ore Inc., the Company’s subsidiary and operator of Bloom Lake, is a “qualified person” as defined by NI 43-101 and has reviewed and approved, or has prepared, as applicable, the disclosure of the scientific and technical information contained in this press release and has confirmed that the relevant information is an accurate representation of the available data and studies for the relevant projects. Mr. Blanchet’s review and approval does not include statements as to the Company’s knowledge or awareness of new information or data or any material changes to the material assumptions and technical parameters underpinning the 2023 Technical Report. Mr. Blanchet is a member of the Ordre des ingénieurs du Québec.
About Champion Iron Limited
Champion, through its wholly-owned subsidiary Quebec Iron Ore Inc., owns and operates the Bloom Lake Mining Complex, located on the south end of the Labrador Trough, approximately 13 km north of Fermont, Québec. Bloom Lake is an open-pit operation with two concentrators that primarily source energy from renewable hydroelectric power. The two concentrators have a combined nameplate capacity of 15 Mtpa and produce low contaminant high-grade 66.2% Fe iron ore concentrate with a proven ability to produce a 67.5% Fe direct reduction quality iron ore concentrate. In January 2023, the Company announced the positive findings of a study evaluating the upgrade of half of the Bloom Lake mine’s capacity to a direct reduction quality pellet feed iron ore and approved an initial budget to advance the project. Bloom Lake’s high-grade and low contaminant iron ore products have attracted a premium to the Platts IODEX 62% Fe iron ore benchmark. The Company ships iron ore concentrate from Bloom Lake by rail, to a ship loading port in Sept-Îles, Québec, and has sold its iron ore concentrate to customers globally, including in China, Japan, the Middle East, Europe, South Korea, India and Canada. In addition to Bloom Lake, Champion owns a portfolio of exploration and development projects in the Labrador Trough, including the Kamistiatusset Project, located a few kilometres south-east of Bloom Lake, and the Consolidated Fire Lake North iron ore project, located approximately 40 km south of Bloom Lake.
Bonterra Resources Inc. (TSX-V: BTR) (OTCQX: BONXF) (FSE: 9BR2) i... READ MORE
Increased facility footprint reflects advanced construction progr... READ MORE
Aris Mining Corporation (TSX: ARIS) (NYSE-A: ARMN) announces the... READ MORE
Zodiac Gold Inc. (TSXV: ZAU) a West-African gold exploration co... READ MORE
Appia Rare Earths & Uranium Corp. (CSE: API) (OTCQB: APAAF) (... READ MORE