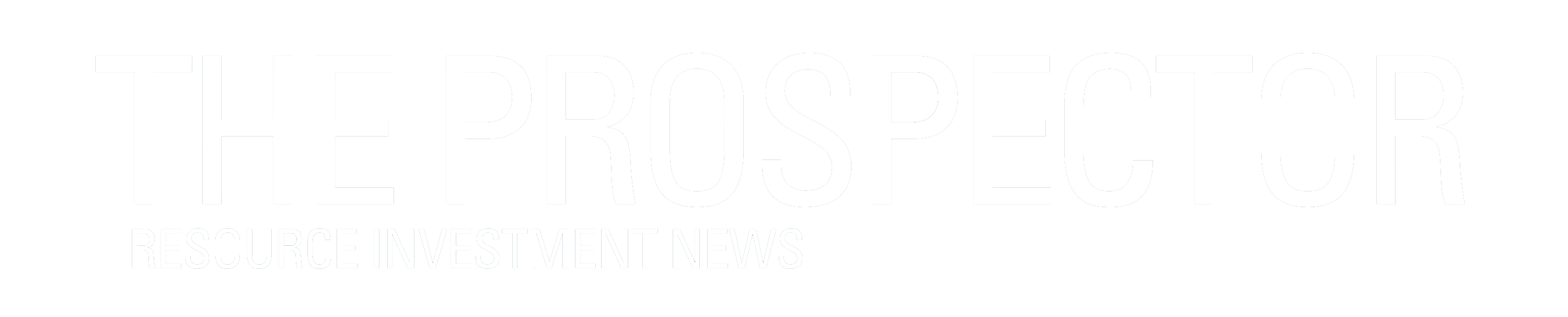
Champion Iron Limited (TSX: CIA) (ASX: CIA) (OTCQX: CIAFF) reports its operational and financial results for its financial first quarter ended June 30, 2024.
Champion’s CEO, Mr. David Cataford, said, “I am proud of our people who efficiently deployed our emergency protocols in response to nearby forest fires. Their actions prioritized the safety of our employees and contractors by completing a rapid preventive evacuation of Bloom Lake and enabled a swift return to site as fires subsided.” Mr. Cataford added, “With respect to our operations, I am happy to report robust quarterly production, record sales and strong financial results for the period. In conjunction with this, we continue to advance our DRPF project, which is expected to significantly reduce emissions in steelmaking, support higher premiums for our products and aligns with the government of Canada’s recent recognition of high purity iron ore as a critical mineral.”
Operations and Sustainability
Financial Results
Growth and Development
During the three-month period ended June 30, 2024, the Company delivered strong operating results with both plants producing at their nameplate capacity. With no major semi-annual shutdowns at the two processing plants and despite a planned two-day annual power interruption during the three-month period ended June 30, 2024, the Company continued to solidify its operations, benefiting from improved mining equipment availability and plants performance, following major maintenance activities completed in the previous quarter. During the three-month period ended June 30, 2024, the Company exceeded its previous record for iron ore concentrate sold. However, as volumes transported continued to be lower than production, the iron ore concentrate stockpiled at Bloom Lake increased by 0.4 million wmt since March 31, 2024, reaching a total of 3.0 million wmt as at June 30, 2024.
The Company continues to seek improvements from the rail operator to receive contracted haulage services to ensure that Bloom Lake’s production, as well as iron ore concentrate currently stockpiled at Bloom Lake, is hauled over future periods.
During the three-month period ended June 30, 2024, the Company continued to analyze work programs and investments required to structurally increase Bloom Lake’s nameplate capacity beyond 15 Mtpa over time. The recently acquired additional mining equipment is expected to support the mine production capacity, as the Company evaluates opportunities to address the bottleneck of operations, and prepare for an increase of stripping activities in the future, per the mine plan. In July 2024, the Company ordered additional railcars to increase rail haulage flexibility over time as part of considerations to potentially increase production beyond Bloom Lake’s existing nameplate capacity.
In June 2024, Société Ferroviaire et Portuaire de Pointe-Noire, a Company’s rail and transshipment service provider, concluded a 5-year collective bargaining agreement with its workers, providing additional stability for the Company’s operations.
Q1 FY25 | Q4 FY24 | Q/Q Change | Q1 FY24 | Y/Y Change | |||
Operating Data | |||||||
Waste mined and hauled (wmt) | 6,733,700 | 6,498,700 | 4 % | 5,198,500 | 30 % | ||
Ore mined and hauled (wmt) | 10,779,300 | 9,471,200 | 14 % | 9,593,500 | 12 % | ||
Material mined and hauled (wmt) | 17,513,000 | 15,969,900 | 10 % | 14,792,000 | 18 % | ||
Stripping ratio | 0.62 | 0.69 | (10) % | 0.54 | 15 % | ||
Ore milled (wmt) | 11,084,300 | 9,349,100 | 19 % | 9,895,600 | 12 % | ||
Head grade Fe (%) | 29.1 | 28.7 | 1 % | 28.8 | 1 % | ||
Fe recovery (%) | 79.3 | 80.2 | (1) % | 78.2 | 1 % | ||
Product Fe (%) | 66.3 | 66.1 | — % | 66.1 | — % | ||
Iron ore concentrate produced (wmt) | 3,876,500 | 3,275,400 | 18 % | 3,397,200 | 14 % | ||
Iron ore concentrate sold (dmt) | 3,442,800 | 2,968,900 | 16 % | 2,563,500 | 34 % |
During the three-month period ended June 30, 2024, 17.5 million tonnes of material were mined and hauled, compared to 14.8 million tonnes during the same period in 2023 and 16.0 million tonnes during the previous quarter, representing an increase of 18% and 10%, respectively. The increased production at the mine site was attributable to higher utilization and availability of mining equipment, and reduced trucking cycle time associated with the construction of additional ramp accesses in the previous quarters.
The stripping ratio of 0.62 for the three-month period ended June 30, 2024, was higher than 0.54 for the same prior-year period, which was negatively impacted by forest fires and, consequently, by the focus on critical activities required to feed the plants. The stripping ratio for the three-month period ended June 30, 2024, was slightly lower than the 0.69 achieved in the previous quarter, when lower mills availability enabled the reallocation of mining equipment to move additional waste materials. The Company plans to maintain higher stripping activities in accordance with the LoM plan over the next quarters.
During the three-month period ended June 30, 2024, the two plants at Bloom Lake processed 11.1 million tonnes of ore, compared to 9.9 million tonnes for the same prior-year period and 9.3 million tonnes in the previous quarter, an increase of 12% and 19%, respectively. Ore processed during the three-month period ended June 30, 2024, was positively impacted by lower maintenance activities, as the major semi-annual shutdowns were performed at both plants during the previous quarter.
The iron ore head grade for the three-month period ended June 30, 2024, was 29.1%, compared to 28.8% for the same period in 2023, and 28.7% during the previous quarter. The variation in head grade was within expected normal variations in the mine plan.
The Company’s average Fe recovery rate was 79.3% for the three-month period ended June 30, 2024, compared to 78.2% for the same period in 2023, and 80.2% during the previous quarter. With continuous efforts made to optimize its recovery circuits, the Company expects ongoing and future work programs to improve recovery rates over time.
With higher Fe recovery and comparable head grade, Bloom Lake produced 3.9 million wmt (3.8 million dmt) of high-grade iron ore concentrate during the three-month period ended June 30, 2024, an increase of 14% compared to 3.4 million wmt (3.3 million dmt) during the same period in 2023, and an increase of 18% compared to 3.3 million wmt (3.2 million dmt) during the previous quarter.
Q1 FY25 | Q4 FY24 | Q/Q Change | Q1 FY24 | Y/Y Change | |||
Financial Data (in thousands of dollars) | |||||||
Revenues | 467,084 | 332,673 | 40 % | 297,162 | 57 % | ||
Cost of sales | 264,911 | 227,496 | 16 % | 208,485 | 27 % | ||
Other expenses | 21,159 | 20,425 | 4 % | 19,645 | 8 % | ||
Net finance costs | 8,259 | 8,831 | (6 %) | 6,926 | 19 % | ||
Net income | 81,357 | 25,791 | 215 % | 16,657 | 388 % | ||
EBITDA1 | 181,160 | 85,099 | 113 % | 65,805 | 175 % | ||
Statistics (in dollars per dmt sold) | |||||||
Gross average realized selling price1 | 171.6 | 166.3 | 3 % | 168.8 | 2 % | ||
Net average realized selling price1 | 135.7 | 112.1 | 21 % | 115.9 | 17 % | ||
C1 cash cost1 | 76.9 | 76.6 | — % | 81.3 | (5 %) | ||
AISC1 | 91.6 | 88.0 | 4 % | 94.1 | (3 %) | ||
Cash operating margin1 | 44.1 | 24.1 | 83 % | 21.8 | 102 % |
Revenues totalled $467.1 million for the three-month period ended June 30, 2024, compared to $297.2 million for the same period in 2023, mainly due to an increase in sales volume to 3.4 million tonnes of high-grade iron ore concentrate, from 2.6 million tonnes for the same prior-year period, representing a 34% increase. Last year’s sales volume was negatively impacted by railway interruptions and reduced services capacity due to the forest fires in June 2023. The year-over-year increase in revenues was also attributable to a 17% increase in the net average realized selling price, driven by positive provisional pricing adjustments on sales recorded during the previous quarter which were finalized at a higher price than expected, and a weaker Canadian dollar offsetting higher freight costs.
Positive provisional pricing adjustments on prior quarter sales of $27.9 million (US$20.8 million) were recorded during the three-month period ended June 30, 2024, representing a positive impact of US$6.0/dmt over 3.4 million dmt sold during the quarter, due to an increase in the P65 index prices early in the period. During the three-month period ended June 30, 2024, a final average price of US$124.2/dmt was established for the 1.8 million tonnes of iron ore that were in transit as at March 31, 2024, and which were provisionally priced at US$112.8/dmt.
The gross average realized selling price of US$125.3/dmt1 for the three-month period ended June 30, 2024, was in line with the P65 index average price of US$126.1/dmt for the period. The 1.8 million tonnes in transit as at June 30, 2024, which were evaluated using an average forward price of US$119.4/dmt, had a negative impact on the gross average realized selling price, which was partially offset by certain sales contracts using backward-looking iron ore index prices, when the index was higher than the P65 index average price for the period. The P65 index premium increased to 12.8% over the P62 index average price of US$111.8/dmt during the quarter, compared to a premium of 11.7% in the prior-year period, mainly impacted by favourable steelmaking profit margins. The P65 index premium over the P62 index in the current quarter was up from a premium of 10.0% in the previous quarter.
Freight and other costs of US$32.1/dmt increased by 24% during the three-month period ended June 30, 2024, compared to US$25.8/dmt in the same prior-year period. This increase was driven by a significantly higher average C3 index of US$25.8/t for the period, compared to US$21.1/t for the same period last year. This can likely be attributed to the conflict in the Red Sea which impacted freight routes during the period, and a much higher demand for vessels in the Atlantic due to the unseasonably elevated supply of iron ore from Brazil. A year-over-year increase in demurrage expenses, resulting from a combination of higher demurrage rates and delayed shipments caused by lower than contracted railway services, also negatively impacted the Company’s freight and other costs during the three-month period ended June 30, 2024.
After taking into account sea freight and other costs of US$32.1/dmt and the positive provisional pricing adjustments of US$6.0/dmt, the Company obtained a net average realized selling price of US$99.2/dmt (C$135.7/dmt1) for its high-grade iron ore shipped during the period.
For the three-month period ended June 30, 2024, the cost of sales totalled $264.9 million with a C1 cash cost of $76.9/dmt1, compared to $208.5 million with a C1 cash cost of $81.3/dmt1 for the same period in 2023, and $227.5 million with a C1 cash cost of $76.6/dmt1 in the previous quarter. Quarterly C1 cash cost per dmt sold was impacted by mining and processing costs, change in concentrate inventory valuation, as well as land transportation and port handling costs incurred during the period.
Mining and processing costs for the 3.8 million dmt produced in the three-month period ended June 30, 2024, totalled $47.9/dmt produced1, representing a significant decrease of 17% compared to $57.6/dmt produced1 in the previous quarter. This improvement in mining and processing costs was attributable to better plants’ performance which positively impacted fixed production costs, as well as lower maintenance activities as the major semi-annual shutdowns of the facilities were performed in the previous quarter. These improvements were partially offset by slightly higher mining costs. Land transportation and port handling costs for the three-month period ended June 30, 2024, represented $25.3/dmt sold1, slightly down from the previous quarter at $26.0/dmt sold1. Fixed costs at the port facilities in Sept-Îles were amortized over a higher sales volume and the Company benefited from volume discounts on port duties. Despite these positive factors, C1 cash cost remained comparable to the previous quarter due to the impact of the change in concentrate inventory valuation. The higher mining and processing costs incurred in the fourth quarter of the 2024 financial year, with lower production volume and higher maintenance activities, have had, and will continue to have, an impact on the cost of sales in upcoming quarters through the change in concentrate inventory valuation.
Mining and processing costs per dmt produced1 for the three-month period ended June 30, 2024, decreased by 5% compared to the same period last year, mainly due to fixed costs amortized over a higher volume of concentrate produced. Land transportation and port handling costs for the three-month period ended June 30, 2024, were also down by nearly $4/dmt sold. The change in concentrate inventory valuation partially offset these decreases.
For the three-month period ended June 30, 2024, the Company generated EBITDA of $181.2 million1, representing an EBITDA margin of 39%1, compared to $65.8 million1, representing an EBITDA margin of 22%1, for the same period in 2023. Higher EBITDA was mainly due to higher gross profit.
For the three-month period ended June 30, 2024, the Company generated net income of $81.4 million (EPS of $0.16), compared to $16.7 million (EPS of $0.03) for the same prior-year period. The year-over-year increase in net income is attributable to higher gross profit partially offset by higher income and mining taxes.
During the three-month period ended June 30, 2024, the Company realized an AISC of $91.6/dmt1, compared to $94.1/dmt1 for the same period in 2023. The decrease was attributable to higher iron concentrate produced and sold, which favourably impacted the Company’s C1 cash cost, offset by higher sustaining capital expenditures mainly related to mining activities, tailings management and mining equipment rebuild program associated with the Company’s expended fleet that were required to support the mine plan in future years. Refer to section 5 — Cash Flows for details on sustaining capital expenditures.
The Company generated a cash operating margin of $44.1/dmt1 for each tonne of high-grade iron ore concentrate sold during the three-month period ended June 30, 2024, compared to $21.8/dmt1 for the same prior-year period. The variation is due to a higher net average realized selling price combined with a lower AISC for the period.
During the three-month period ended June 30, 2024, the Company maintained all of its properties in good standing and did not enter into any farm-in/farm-out arrangements. During the three-month period ended June 30, 2024, $2.6 million in exploration and evaluation expenditures were incurred, compared to $2.7 million for the same prior-year period. During the three-month period ended June 30, 2024, exploration and evaluation expenditures mainly consisted of work done in Newfoundland and Labrador
Details on exploration projects and maps are available on the Company’s website at www.championiron.com under the Operations & Projects section.
Three Months Ended | ||||
June 30, | ||||
2024 | 2023 | |||
(in thousands of dollars) | ||||
Tailings lifts | 16,104 | 11,946 | ||
Stripping and mining activities | 10,325 | 3,263 | ||
Mining equipment rebuild and replacement | 10,373 | 4,552 | ||
Other sustaining capital expenditures | 1,206 | 42 | ||
Sustaining capital expenditures | 38,008 | 19,803 | ||
DRPF project | 58,465 | 11,083 | ||
Other capital development expenditures at Bloom Lake | 18,988 | 24,784 | ||
Purchase of property, plant and equipment as per cash flows | 115,461 | 55,670 |
Sustaining Capital Expenditures
Sustaining capital expenditures were $11.0/dmt sold for the three-month period ended June 30, 2024, compared to $7.7/dmt for the same prior-year period. This 43% increase reflected the additional mining development, equipment rebuild and tailings lifts required to support additional production over the LoM.
The increase in tailings-related investments is part of the Company’s long-term plan to prepare the site for the LoM operations with Bloom Lake’s increased nameplate capacity. As part of its ongoing and thorough tailings infrastructure monitoring and inspections, the Company continues to invest in its safe tailings strategy and is implementing its long-term tailings investment plan. The Company’s tailings work programs are typically completed in the first half of the financial year due to more favourable weather conditions.
The increase in stripping and mining activities for the three-month period ended June 30, 2024, was attributable to mine development costs, including topographic and pre-cut drilling work, as part of the Company’s mine plan. Last year’s stripping and mining activities were negatively impacted by limited equipment availability. No stripping costs were capitalized during the three-month period ended June 30, 2024 ($0.3 million for the same prior-year period).
The increase in the Company’s mining equipment rebuild program for the three-month period ended June 30, 2024, was attributable to the major overhaul of its growing mining fleet over the last two years, driven by the Company’s expansion. The mining equipment rebuild and replacement program is in line with the Company’s fleet management program for the 2025 financial year.
DRPF Project
During the three-month period ended June 30, 2024, $58.5 million was spent in capital expenditures related to the DRPF project. Investments mainly consisted of on-site preparation activities, engineering work, long lead-time equipment purchasing and finalization of the construction of the lodging complex. Cumulative investments of $153.8 million were deployed on the DRPF project as at June 30, 2024, with an estimated total capital expenditure of $470.7 million, as per the project study released in January 2023.
Other Capital Development Expenditures at Bloom Lake
During the three-month period ended June 30, 2024, other capital development expenditures at Bloom Lake totalled $19.0 million ($24.8 million for the same period last year), including $10.2 million in infrastructure improvements and conformity ($8.4 million for the same prior-year period), $3.8 million for the mine maintenance garage expansion to support the expanded truck fleet ($8.4 million for the same prior-year period), and $2.8 million in deposits for mining equipment ($6.6 million for the same prior-year period).
About Champion Iron Limited
Champion, through its wholly-owned subsidiary Quebec Iron Ore Inc., owns and operates the Bloom Lake Mining Complex, located on the south end of the Labrador Trough, approximately 13 km north of Fermont, Québec. Bloom Lake is an open-pit operation with two concentrators that primarily source energy from renewable hydroelectric power. The two concentrators have a combined nameplate capacity of 15 Mtpa and produce low contaminant high-grade 66.2% Fe iron ore concentrate with a proven ability to produce a 67.5% Fe direct reduction quality iron ore concentrate. Benefiting from one of the highest purity resources globally, the Company is investing to upgrade half of the Bloom Lake mine capacity to a direct reduction quality pellet feed iron ore with up to 69% Fe. Bloom Lake’s high-grade and low contaminant iron ore products have attracted a premium to the Platts IODEX 62% Fe iron ore benchmark. The Company ships iron ore concentrate from Bloom Lake by rail, to a ship loading port in Sept-Îles, Québec, and has delivered its iron ore concentrate globally, including in China, Japan, the Middle East, Europe, South Korea, India and Canada. In addition to Bloom Lake, Champion owns a portfolio of exploration and development projects in the Labrador Trough, including the Kami Project, located a few kilometres south-east of Bloom Lake, and the Cluster II portfolio of properties, located within 60 km south of Bloom Lake.
Highlights Assays received High-grade assays returned for Drill H... READ MORE
Kenorland Minerals Ltd. (TSX-V: KLD) (OTCQX: KLDCF) (FSE: 3WQ0) a... READ MORE
Wallbridge Mining Company Limited (TSX: WM) (OTCQB:WLBMF) announc... READ MORE
Provides Update on Pedra Branca PGE Project and Strategic Growth ... READ MORE
Pasinex Resources Limited (CSE: PSE) (FSE: PNX) announced financi... READ MORE